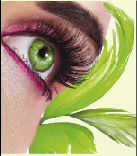
SEE Live Production:
Tankefel inom elektronikindustrin
Elektronikindustrin har existerat i knappt 70 år vilket kan jämföras med bilindustrin som introducerade sina första bilar för mer än 140 år sedan. Elektronikindustrin är jämfört med bilindustrin rena barnet men det finns många likheter och olikheter. Låt oss starta med att göra en förenklad och fiktiv liknelse mellan bilens chassi (underrede) och ett kretskort.
Ladda ner artikeln på 500 kbyte här (länk, pdf). |
I båda fallen sker starten från en bottenplatta/mönsterkort för att därefter bygga på olika delar. En bil består av cirka 5 000 delar vilket kretskorten endast har i extrema fall. Dagens bilar köps av en marknad som är kvalitetsmedveten och känslig mot driftstörningar. Detta faktum har bilindustrin anammat och satsar stora summor på att utveckla en plattform som skall motsvara kundernas krav samt gemensamt kommit överens om konstruktions- och produktionsstandarder som de flesta bilbyggare följer till punkt och pricka. Inom elektronikindustrin finns det IPC-standarder och -rekommendationer för hur mönsterkortet bör utvecklas och caddas, men de flesta föredrar sina egna regler. Detta leder i alltför många fall till att mönsterkortstillverkaren får gråa hår i förtid och att mönsterkortets kvalitet inte lever upp till en förväntad IPC-klass.
Finns det några exempel på detta förfarande? Vi frågar Rikard Wallin, vd på NCAB Group Sweden.
– För en tid sedan kom ett elektronikkonstruktionsföretag till oss med ett avancerat mönsterkort som vår interna CAM-avdelning betraktade som omöjligt att genomföra. Kunden hade dålig kunskap om IPC-2220 och insisterade på att kortet skulle byggas enligt underlagen. Vi drog oss inte ur utan startade produktionen. Som befarat fungerade inte mönsterkorten, det var bara att slänga. Projektet havererade för denna kund då slutkunden valde att avsluta samarbetet med dem.
Finns det några exempel på detta förfarande? Vi frågar Mats Pettersson, försäljningschef på Teltex.
– Allmänt är bättre underlag högsta prioritet. En specifikation bör bland annat innehålla total korttjocklek, koppartjocklekar på ytor och hål, ytbehandling (HAL, ENIG, etc)och basmaterial enligt IPC-4101D. Specifikt så har vi störst problem med lödmasken mellan footprint som ligger för nära varandra. Minimum bör vara 100 µm för att få fullgod vidhäftning. Vårt avstånd mellan lödmask och kanten på lödytan är 50 µm vilket ger ett minimum av 200 µm mellan lödpaddarna för att lödmasken skall få plats. Konsekvensen av för små avstånd är en lägre yield och att kretskortstillverkaren får kvalitetsproblem med exempelvis lodkulor och lodbryggor och kan inte leverera kretskorten enligt IPC-A-610F Klass 2 eller 3.
S.E.E. 2016 är Nordens största och viktigaste mötesplats för den professionella elektronikindustrin och går av stapeln på Kistamässan den 19–21 april 2016. Dragplåstret är en avdelning för tvätt, renhetsmätning och lackning av flera hundra avancerade kretskort som tillverkas i två stycken ytmonteringslinor på mässgolvet. I anslutning arrangeras SM i Handlödning samt Handlödning för studenter. |
Som bekant är fukt och salter ovälkomna riskfaktorer när det gäller bristande funktion på grund av läckströmmar och korrosion. Bilindustrin har utvecklat metoder för att minska riskerna medan elektronikindustrin med få undantag låtsas som de inte finns.
På bilens bottenplåt placeras en rad detaljer för att yielden på slutprodukten skall vara i närheten av sex sigma. Biltillverkare världen över har också insett att detaljerna kan köpas externt medan själva slutmonteringen inte lämpar sig att lägga ut på lego.
Elektronikindustrin däremot placerar sina detaljer (komponenter och kontaktdon) på en yta (pad eller footprint) som i flertalet fall definieras av godtycklighet eller av komponenttillverkarens teoretiska beräkningar. I tillägg gäller det att lägga ut montering, lödning och tvättning så långt från ens egen konstruktionsavdelning som det är möjligt och dessutom flytta runt den när galoscherna inte passar längre. Resultatet är att elektronikindustrins yield räknas i värsta fall till tvåsiffriga procenttal med kvalitetsbrister och höga kostnader som resultat.
Vilka fakta grundar sig rekommendationerna för footprint på era komponenter? Vi frågar Martin Danielsson, försäljningschef på Würth Elektronik Sweden.
– Vi avsätter mycket tid i laboratoriet för att testa lödning och utformning av mönsterkortens footprint för våra nya komponenter. Detta görs i våra egna labb med hjälp av internationellt standardiserade lödprofiler från t.ex. J-STD-020 och J-STD-075. Detta har medfört att våra footprint för ytmonterade chipkomponenter är mindre än komponenten för att undvika bland annat Tomb Stone. För större och tyngre passiva komponenter är footprintrekommendationen större för att komponenten ska kunna tåla stötar och vibration.
Ytterligare ett steg framåt är sammanfogningstekniken där elektronikindustrin använder mjuklödning med hjälp av lodpasta medan bilindustrin föredrar skruv, mutter och svetsning. De senare är väl beprövade metoder medan mjuklödning med hjälp av lodpasta endast har 25–30 år på nacken. Svagheten ligger i överföringen av lodpasta till mönsterkortet, så kallad screentryckning med hjälp av en stencil eller som alternativ jetprintning utan stencil. Det gäller att både ha rätt positionering och volym för att kunna uppnå IPC Klass 2 eller 3, vilket inte är helt enkelt att upprepa under lång tid och stora serier.
Vilka fördelar finns det med screentryckning med hjälp av en etsad stencil jämfört med en laserskuren stencil?
Vi frågar Göran Karlström, key account manager på HP-Etch.
– Aperturerna etsas samtidigt, de får runda hörn, inga grader och tillsammans med en kontrollerad släppvinkel ger det bästa möjliga förutsättning för tryckning av lodpasta. Flera olika tjocklekar på samma stencil och extra hål utan kostnad (Tension relief) är andra faktorer som förbättrar yielden och därmed ökar screentryckskvaliteten vilket är viktigt för att erhålla lödfogar enligt IPC-A-610F Klass 2 eller 3.
På den ekonomiska sidan är skillnaden att bilindustrin av empiriska erfarenheter genom årtionden upptäck att bilens plattform är grunden till kvalitet och funktionsduglighet. Elektronikindustrin har ännu inte insett sambandet mellan kvalitet och pris.
När dagens bilar är fullproppade med elektronik uppstår en kulturchock hos bilindustrin då det gedigna produktions- och mekanikkunnandet möter den flummiga elektronikvärlden. Resultatet kan inte bli annat än fler missnöjda bilägare, men det finns en stor förbättringspotential, det är bara att lära från bilindustrin.
På S.E.E. 2016 kommer hundratals kretskort att produceras live samt tvättas och lackas för att därefter undersökas i en mängd olika parametrar som i sin helhet redovisas på Tillförlitlighetskonferensen den 8 september 2016 på Stockolmsmässan.