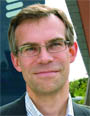
– Det var den skillnaden som fick Ericssons ledning att ändra strategi säger Björn Ekelund.
Investeringarna i 3G-mobiler måste spridas över flera telefontillverkare på liknande sätt som halvledartillverkarna lagt över produktionen av kretsar på foundries. Insikten ledde fram till att EMP bildades år 2001. För produktionen av själva telefonerna gick Ericsson som bekant samman med Sony i ett hälftenägt bolag, som är granne med EMP i Lund.
Björn Ekelund Titel: Chef för produktplanering och strategisk teknikutveckling Född:1961 Bor: I Bjärred utanför Lund Familj: Gift och tre barn Karriär: Har varit på Ericsson sedan licentiatexamen 1987. Har haft fler jobb än jag kan komma ihåg. Intressen: Tränar kickboxing och spelar World of Warcraft Dold talang: Var i början på 80-talet bland Sveriges bästa i morsetelegrafi |
– Det har tillverkats över 250 miljoner telefoner baserade på Ericssonteknologi sedan vi startade 1985 och i dessa finns över en miljard asicar som vi konstruerat, säger Björn Ekelund.
Spridda över hela världen
För att utveckla asicarna, den tillhörande mjukvaran och för att ge kunderna support har plattformsbolaget cirka 1800 anställda spridda på kontor över hela världen.
Att EMP är en viktig del av Ericsson totalerbjudande indikeras också av att enheten alltid är med vid utvecklingen av ny teknik för mobilnäten.
– Deras produktplaner och våra produktplaner är synkroniserade. I slutänden styrs det av koncernledningen, men det är en ständig dialog. Det gör att Ericsson kan säga till sina kunder: Vi har koll på hela kedjan och ni kan få billiga telefoner.
Eftersom EMP säljer en plattform och inte färdiga telefoner kan vilken logotyp som helst finnas på telefonen, som kan vara en billig kontantkortstelefon eller en dyr handdatorlikanande telefon. Båda varianterna kan vara baserade på samma plattform.
Björn Ekelund tar Sony Ericssons handdatorliknande flaggskepp P990 och den enkla kontantkortstelefon från Sagem kallad My W7 som exempel. Båda är 3G-telefoner som baseras på plattformen U100.
För att klara det krävs att plattformen går att konfigurera på olika sätt. I den avancerade versionen finns till exempel extrakretsar som hanterar grafiken.
Samma mjukvara på alla plattformar
En stor produktportfölj är en viktig nyckel till framgång för alla mobiltelefontillverkare. Samtidigt kostar varje ny modell mycket att utveckla så det är hela tiden en delikat balansgång.
– Den absolut dyraste komponenten i telefonerna idag är mjukvaran. Vi har tagit fasta på det för att skydda kundernas investeringar.
Rent konkret innebär det att kunderna kan ta fram en GSM-modell, en Edge-modell och en 3G-modell med i stort sett samma mjukvara. Dessutom är plattformarnas gränssnitt i princip oförändrade mellan de olika generationerna vilket gör att kunderna kan återanvända sin mjukvara. Just att mjukvaran är den största komponenten i plattformen återkommer Björn Ekelund ständigt till.
– När vi började jobba med 3G så såg vi att mjukvaruinnehållet skulle explodera. Det var som ett sädesfält framför oss och så stod vi där med nagelsaxen, säger han och sträcker ut armarna för att visa på problemet.
Kan både hårdvara och mjukvara
De bästa chipsen designas enligt honom av dem som är duktiga på just mjukvara. För då vet man hur chipsen kommer att användas, och kan optimera för saker som strömförbrukning, datagenomströmning (throughput) och avbrottstider (interrupt latency).
– En av våra unika fördelar är att vi kan båda delarna. Vi brukar prata om systemdesign och systemkunnande. Där ligger vi väldigt långt framme.
Kostnaderna för att utveckla hårdvaran rakar förvisso också i höjden för varje ny processgeneration. Det gäller både utvecklingsarbetet och startkostnaderna för en asic. Men att det skulle finnas någon mur som sätter stopp för utvecklingen kan Björn Ekelund inte se.
– Kostnadsökningarna kan bromsa upp utvecklingen, men vi har samtidigt volymerna så vi ser inget slut på det.
EMP har redan designat kretsar på 65 nm, de kommer i plattformen U330 nästa år. Och man har också börjat titta på nästa processnod, som är 45 nm.
Några egna konstruktionsverktyg gör inte EMP. Allt köps in, och man använder ”rätt säkra kort” enligt Björn Ekelund. Han påpekar att EMP får tidiga releaser från leverantörerna.
– Vi är visserligen mycket mindre kunder till EDA-tillverkarna än till exempel pc-processortillverkarna men vi tänjer gränserna inom andra områden som kiselyta och strömförbrukning.
Den teknik som EMP hjälper till att driva fram är användbar även inom andra områden vilket förklarar verktygsleverantörerna intresse.
Avslöjar inga leverantörer
Exakt vilka EDA-leverantörer man använder är dock hemligt, liksom vilket språk man konstruerar i liksom så mycket annat när det gäller detaljer. Men enligt Björn Ekelund använder sig EMP av verktyg från de flesta större leverantörer. Om det även inbegriper svenska Virtutech går heller inte att få bekräftat men EMP använder simuleringsverktyg som emulerar hårdvaran.
– Vi kan ta riktig kod och köra den för att se saker som om cachen är stor nog eller om processorkraften äts upp av alla avbrott, exemplifierar han.
En annan viktig aspekt är hur man delar upp arbetet mellan hårdvara och mjukvara.
– Vi använder också vårt kunnande om till exempel luftgränssnitten och vilka timingkrav som finns där för att styra vad som läggs i hårdvara och vad som läggs i mjukvara. Dessutom kan det vara så att du inte vet allt för att det inte är färdigstandardiserat och då läggs det i mjukvara.
Förutom EDA-verktyg använder sig EMP av FPGA-plattformar för att ta fram prototyper till delar av asicarna. En hake är dock att FPGA-korten inte klarar full hastighet.
Har omfattande bibliotek men testfall
Precis som hos andra asictillverkare är verfiering den stora arbetsinsatsen. Plattformarna utsätts dessutom för systemtest där EMP samlat på sig runt 15 000 olika testfall för allt från olika moduler och delsystem till hela plattformen. På det kommer sedan interoperabilitetstester hos både infrastrukturtillverkare och operatörer. De senare blandar utrustning från olika leverantörer och optimerar också näten på olika sätt.
– Man kan driva testandet hur långt som helst men det gäller att hitta en bra avvägning mellan risk och kostnad. Det är inte så lyckligt att alla de kretsar vi designat varit 100 procent rätt, men de har alltid varit bra nog, säger Björn Ekelund.
De avvikelser man hittar kan normalt hanteras av mjukvaran. Att använda FPGA:er för att komplettera asicarna är inte aktuellt. Kostnaden blir helt enkelt för hög jämfört med en asic, som kräver betydligt mindre kiselyta för att utföra samma uppgift.
För utveckling och test av applikationsprogrammen använder plattformsbolaget Eclipse som ramverk. Kunderna kan provköra applikationer i EMP:s api-emulator, som är en integrerad del bolagets Eclipsbaserade utvecklingsmiljö, innan hårdvaran finns framme.
Blandar eget med eget inköpt
EMP utvecklar egna IP-block för vissa nyckelområden som är mobiltelefonspecifika. Det gäller bland annat radiomottagare men även multimediateknik där effektförbrukning måste hållas nere och där minnestillgång är begränsad.
– Vi köper också in IP som inte differentierar produkten, till exempel en UART, en DMA-kontroller eller en ARM-kärna.
Dessa IP-block sätts sedan ihop i asicar.
– Vi pratar om att vi har ett chassi som bestyckas. Och chassit uppgraderas ständigt eftersom det behövs mer bandbredd för data medan IP-block återanvänds i hög grad.
Som exempel tar han U300 som lanserades i våras. Den har fått viss ny arkitektur jämfört med U100 men radiotekniken är den samma.
– Vi är övertygade om att U300 är den kostnadseffektivaste 3G-lösningen på marknaden. Det gäller både kiselyta och implementeringskostnaden för kunderna. En del av våra konkurrenter kommer från kiseltillverkarhållet och tenderar att fokusera på kretsarna. Vi har en bakgrund som telefontillverkare och talar gärna om totallösningen och hur vi gör den så billig som möjlig.
Minst är inte alltid bäst
Enligt Björn Ekelund kan det ibland gå att spara pengar genom att göra kretsarna något större och dyrare än vad som är nödvändigt.
– Det kan vara en regulator eller något annat smått som är knöligt att göra och där man kanske kan spara en dollar på telefonen genom att göra kretsarna 10 cent dyrare.
Fler försäljningsargument
Bakgrunden som telefontillverkare innebär också att det finns kunskap om produktion och kalibrering. Även det något som är ett säljargument.
– Vi lägger en hel del energi på att göra våra lösningar producerbara.
Som ett exempel tar han uteffekten på sändaren som ska ha ett antal steg och varje steg ska ligga inom 0,2 dB. Det finns fem, sex parametrar att skruva på vilket gör det till ett mångdimensionellt kalibreringsproblem.
– Vi utvecklar en algoritm för att ställa in nivåerna på ett effektivt sätt. Och eftersom vi gjort chipsdesignen så kan vi göra algoritmen bättre än någon annan.
Sen spelar det inte så stor roll hur mön-sterkortet som kunden designat ser ut eller vilket slutsteg eller SAW-filter kunden valt.
– För det mesta använder kunderna vår rekommendera lösning rätt av.
Det gäller särskilt när plattformen är ny och därmed tänjer gränserna för vad som är möjligt. Efter sex till åtta månader finns det i regel fler komponenter att välja på. Och kunderna börjar då byta ut vissa komponenter.
EMP ger också kunderna förslag på vilken testutrustning de ska använda och i vilken ordning testerna ska ske.
– En plattform kanske har 200 testpunkter och vi vet vilka som hänger ihop. Är nummer 26 OK så behöver man inte testa 28 och fallerar nummer 13 och 22 är OK så är det ändå OK.
Från sju till tre asicar
Den första 3G-plattformen från EMP – U100 – hade sju asicar, varav tre för radion, två för det digitala basbandet och två för det analoga basbandet. Idag är det reducerat till tre: en för radion, en digitalkrets för basbandet och en analogkrets för basbandet. Att man lyckats med det beror inte bara på att kiselteknologin gjort framsteg, de många kretsarna i U100 berodde också på att EMP ville minimera riskerna.
– Det går fortare att utveckla i flera chip, det finns en helt annan observerbarhet. Och kom ihåg att U100 började designas år 2000 så chippen blev ganska stora trots att de var ganska många.
En annan orsak till att det blev sju chips var att man ville ha en modulär lösning. Genom att ta bort ett digitalt basbandschips och två radiochip fick man en GPRS-telefon och genom att lägga till ett digitalt basbandschips blev det en Edge-telefon.
Tiden inte mogen för enkretslösning
På GSM-sidan börjar det komma enkretslösningar där både radio och basband ligger i samma krets. Och Bluetooth liksom wlan har länge tillverkats som enkretslösningar.
– Naturligtvis kommer det singelchips för 3G också, men kraven på radioprestanda och processorkapacitet är betydligt lägre för de andra teknikerna. Wlan är en ganska primitiv teknik i jämförelse 3G som ska klara fading, hand-over med mera.
Ytterligare en förklaring till att 3G-lösningarna behöver delas upp är anslutningarna.
– Ett basbandschips har runt 300 anslutningar och det skulle nästa explodera och ge en kapsel som är större än tre separata om man integrerade dem till en enda.
De CMOS-processer som används för de tre kretsarna är därtill optimerade på olika parametrar.
– Det finns en sweet-spot som ligger runt 30 till 40 kvadratmillimeter. Gör man kretsar som är större än det är det inte ekonomiskt längre.