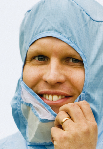
– De kommer att outsourca så fort det finns någon som kan köra åttatumsskivor, säger Edvard Kälvesten som var med att grundade Silex år 2000.
Han kallar dem Analog Devices-kunder, företag som i likhet med Analog Devices har egna halvledarfabriker men som har problem med lönsamheten. Det kan till exempel vara avlagda CMOS-fabriker med åttatumsprocesser som konverterats till mikromekanik.
FAKTA ”Kapseln” utgörs av ett lock i form av en kiselskiva som har samma storlek som den odelade skivan med komponenter. I det blivande locket etsar man bort material så att det skapas urgröpningar som ger plats för de mikromekaniska komponenterna. Där man vill ha väggar etsar man istället tunna genomgående hål som pläteras. På de ytor i locket där det finns viahål och som ska bondas ihop med skivan med kretsar lägger man guld. Även på skivan med kretsarna lägger man guld på dessa ställen. Genom att trycka ihop skivorna och värma smälter guldet ihop och bildar en hermetisk fog. Processen klarar sig med en temperatur under 400 grader Celsius vilket innebär att man kan kapsla mikromekaniska komponenter som placerats ovanpå en skiva med komponenter i CMOS utan att dessa förstörs. Skivan sågas sedan upp och komponenterna kan till exempel monteras som flip chip. |
Ett annat argument för åtta tum är att totalkostnaden för den färdiga elektronikprodukten sjunker om man kan integrera mikromekaniska komponenter ovanpå logikkretsarna.
– Företagen kan komma till oss med sina åttatumsskivor med CMOS-kretsar och sedan kan vi lägga på de mikromekaniska komponenter och kapsla.
Ökar integrationsgraden
Tekniken används bland annat för att placera till exempel resonatorer, accelerometrar och gyron ovanpå logiken och därmed få billigare system.
– Vi driver den utvecklingen, säger Edvard Kälvesten när han visar runt i det som är på väg att bli en fabrik.
Än så länge är det nya renrummet på 800 kvadratmeter ett tomt skal men i litografirummet står en ouppackad stepper från holländska ASML. I korridoren finns ytterligare några nya maskiner och den sista ska vara på plats under mars månad.
– Vi kommer att kunna göra geometrier ner till 0,5 µm.
Därmed tar företaget ett processtekniskt kliv framåt på 20 år och hamnar på ungefär samma nivå som halvledarindustrin befann sig i början av 2000-talet.
Att det går att rita smala linjer är dock inte det viktigaste argumentet, istället handlar det om den bättre noggrannhet som de finare geometrierna medför. Ytterligare ett argument är att ”Analog Devices-kunderna” har fabriker som klarar 0,5 µm. Med en lina som klarar samma geometrier blir det enklare för Silex att locka över dem när de inte behöver konstruera om sina kretsar.
Ytterligare ett ess i rockärmen är att företaget har en patenterad process för att kapsla de mikromekaniska komponenterna redan på skivan, så kallad Wafer Level Packaging, WLP, se ruta.
Max en partikel per kubikfot
Det nya renrummet som byggts speciellt för åttatumslinan är snäppet bättre än det gamla.
– Det kommer att hålla klass 1 till större delen medan vårt gamla renrum till största delen håller klass 100.
Den högre renheten bidrar till att förbättra yielden. Dessutom är den nya linan helt automatiserad. I den gamla sextumslinan är man tvungen att plocka upp skivorna manuellt ur kassetterna i vissa moment. Då finns alltid risken att man tappar dem, repar dem eller att det kommer damm på dem.
För att finansiera bygget tog Silex in 150 miljoner kronor i riskkapital förra året. Även om det är extrem lågkonjunktur idag och ytterst få köper nya maskiner innebär det inte att det blir pengar över.
– Vi får helt enkelt bättre maskiner än vad vi hade kunnat köpa om det varit högkonjunktur.
Den nya linan är komplett med alla processteg. Det enda man inte behöver investera i är infrastrukturen i form av bland annat ventilation, gaser och vatten som delas med den äldre delen av fabriken som är på cirka 1 000 kvadratmeter.
Fyra masker i genomsnitt
Den nya linan fyrdubblar kapaciteten från cirka 100 000 masklager till 400 000 masklager per år. Hur många tillverkade kiselskivor det motsvarar beror på hur komplicerade kretsarna är.
Medan man vid tillverkning av CMOS-logik kan behöva mellan 15 och 30 masklager använder Silex kunder mellan en och 18 masker.
– Medel har gått upp från tre till fyra eftersom allt fler av våra kunder även kapslar hos oss.
Beslutet om att bygga ut fattades i fjol när kapaciteten i den gamla fabriken var på väg att slå i taket. Men lågkonjunkturen har medfört att ökningen stannat av.
– Om det inte tar fart mot slutet av året räknar vi med samma omsättning i år som i fjol, säger Edvard Kälvesten.
Då landade det runt 170 miljoner kronor. För 2009 kommer inkörningen av den nya fabriken att medföra en mindre förlust.