Swerea IVF
Vem har ansvaret för tillförlitligheten i kretskort?
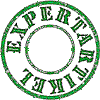
![]() Fler tekniska rapporter finns på etn.se/expert |
Problemet är att de standarder som normalt används för att säkerställa kvaliteten på elektronikhårdvara inte har krav på den typen av testning. Komponenttillverkare kvalificerar i allmänhet sina komponenter enligt JEDEC JESD47. Detta är en standard som specificerar ett antal stresstest som utförs på lösa komponenter. Livslängden på lödfogarna är därför inte något som komponenttillverkarna normalt utvärderar. Det finns visserligen en JEDEC-standard för att testa inlödda komponenter men jag har inte hittat någon komponenttillverkare som angett att komponenter har kvalificerats enligt denna standard.
Kretskortstillverkare har oftast krav på att tillverkningen ska uppfylla kraven i IPC J-STD-001 och/eller IPC-A-610. Dessa standarder har i stort sett enbart visuella krav på lödfogarna. Uppfyllande av kraven i IPC:s standarder säkerställer därför inte att lödfogarna kommer att ha tillräcklig livslängd, vilket också påpekas i andra IPC-dokument.
Risken är därför stor att det blir slutanvändaren som får upptäcka problem med otillräcklig livslängd av lödfogar. Så vem har egentligen ansvaret för slutproduktens tillförlitlighet?
Alla verkar förlita sig på att om alla följer tillämpliga (traditionella) standarder så kommer slutprodukten per automatik bli tillförlitlig. Man utgår ifrån att de är relevanta och tillräckliga för att säkerställa tillförlitligheten. Detta utan att egentligen känna till bakgrunden till dessa standarder och deras begränsningar. I princip innebär detta att man lägger ansvaret för tillförlitligheten på tredje part, de organisationer som utvecklar standarderna, en part som man aldrig kommer kunna ställa till svars.
För att förstå hur det har blivit så här behöver man känna till hur standarder har utvecklats under de senast femtio åren och vad som var det ursprungliga syftet. Efter andra världskriget och fram till och med åttiotalet utvecklades ny teknik för militära produkter. Den utvecklade tekniken var mycket robust och så länge man hade bra kontroll på tillverkningsprocesserna kunde man förvänta sig att produkterna höll längre än den förväntade livslängden. Fokus kom därför att ligga på tillverkningsprocesserna.
För att säkerställa en jämn och hög tillverkningskvalitet tog man i USA fram ett stort antal militära standarder som i detalj reglerade hur material, komponenter, mönster- och kretskort skulle tillverkas och kvalificeras. Man tog även fram standarder för hur tillförlitligheten av slutprodukten skulle predikteras och verifieras. Metodiken för att göra detta beskrevs i detalj i MIL-STD-338. Där angav man i inledningen att metodiken baserades på två antaganden. För det första antog man att felintensiteten var konstant under produktens hela förväntade livslängd och för det andra att fel nästan uteslutande orsakades av tillverkningsdefekter i halvledarkomponenter.
Det första antagandet innebar att man utgick ifrån att inga utmattnings- och åldringsfel skulle komma att uppstå under produktens förväntade livslängd. Då fanns det inte någon anledning att ta fram test som var designade för att utvärdera den typen av fel. De test som krävdes för att verifiera tillförlitligheten av slutprodukten var i stället designade för att efterlikna driftsmiljön. Kravet var sedan att man testade tills man fått ett statiskt säkerställt värde på den konstanta felintensiteten. Därför var det likvärdigt att testa 1 enhet under 100 timmar som att testa 100 enheter under 1 timma.
Detta förutsatte som nämnts att man säkerställde en hög och jämn kvalitet på material, komponenter med mera genom att i standarder reglera i detalj hur dessa skulle tillverkas och testas. Eftersom man även antagit att fel nästan uteslutande orsakades av tillverkningsdefekter i halvledarkomponenter var det främst för dessa som man hade krav på omfattande testning. Denna testning bestod av stresstester specificerade i MIL-HDBK-883 (JEDEC JESD47 är i stort sett en kopia av denna). Testerna var designade för att upptäcka defekter i komponenterna Om man ändrade i tillverkningen av en komponent efter att man kvalificerat den krävdes en omkvalificering.
Detta innebar att den utvecklade tekniken var mycket robust och kraftigt överdimensionerad för kommersiella tillämpningar. Det räckte därför att säkerställa att produktionen var någorlunda under kontroll för att produkten med råge skulle klara förväntad livslängd. De standarder som används idag i hela produktframtagningskedjan för kommersiella produkter har sitt ursprung i dessa militära standarder och bygger på samma två antaganden, även om det inte finns uttryckt någonstans.
Det som orsakade tillförlitlighetsproblem var dåliga designlösningar och tillverkningsdefekter. De kvalificeringstest som togs fram för högtillförlitlighetsprodukter var därför konstruerade för att hitta denna typ av defekter och inte fel som orsakades av åldring/utmattning. För många produkter med lägre tillförlitlighetskrav utfördes ingen testning alls. Eftersom fokus i standarderna var på att undvika tillverkningsdefekter kom huvudansvaret för kvaliteten i de flesta branscher att hamna på de som utför produktionen. För lödfogar till hålmonterade och benförsedda komponenter räckte det i allmänhet med en visuell avsyning för att upptäcka dåliga lödfogar.
Idag är det inte längre militärindustrin som leder utvecklingen av ny teknik utan den kommersiella marknaden och då främst för produkter med kort förväntad livslängd och relativt låga tillförlitlighetskrav, som spelkonsoler, datorer och mobiltelefoner. Fokus är på så hög funktionalitet som möjligt till så lågt pris som möjligt. För halvledarkomponenter innebär detta att man har gått från benförsedda komponenter som DIL- och QFP-komponenter till benlösa komponenter som BGA- och QFN-komponenter. Den högre funktionalitet som man uppnått är till priset av kortare livslängd för lödfogarna.
En grov uppskattning av antalet cykler mellan –40 och 125 °C som lödfogarna till de olika komponenterna klarar är för QFP >10 000, BGA 3 000 till 8 000 och QFN 1 000 till 3 000 cykler [1]. Användning av ny ingjutningsplast (se tidigare artikel) kan ytterligare korta livslängden för BGA- och QFN-komponenter liksom minskning av pitchen för BGA komponenter till 0,5 mm eller mindre. Än värre, lackning av BGA- och QFN-komponenter kan sänka livslängden av dessa ytterligare med upp till 85 procent.
Detta innebär att för många produkter med BGA- och QFN-komponenter kan man förvänta sig att utmattningsbrott kan uppstå i lödfogarna under den förväntade livslängden. Men det är inte bara risken för utmattningsbrott som har ökat utan även för andra typer av åldringsfel som t ex sprödbrott i lödfogar, brott i hålpläteringar, läckströmmar och CAF. Den förväntade felintensitet som funktion av tiden ser därför annorlunda ut för dagens elektronikprodukter men standarderna för att säkerställa tillförlitligheten har inte förändrats. De utgår fortfarande från att det är tillverkningsdefekter som är orsaken till otillräcklig tillförlitlighet (första och andra fasen i badkarskurvan).
Detta är skälet till att de standarder som idag används för att säkerställa tillförlitligheten inte är relevanta för dagens teknik, inklusive de standarder som fordonstillverkare utgår från för att specificera krav för att kvalificera slutprodukten. Även dessa test har sitt ursprung i MIL-standarder designade för att hitta dåliga designlösningar och tillverkningsdefekter.
I början av nittiotalet konstaterade amerikanska militära myndigheter att det traditionella arbetssättet att säkerställa tillförlitlighet inte levererade vad det förväntades leverera ”reliable and state-of-the-art products”. Därför genomförde försvarsdepartementet i USA 1994 ”The Military Specifications and Standards Reform” enligt vilken man skulle ha en ”Performance-based Approach to Reliability”. Detta har resulterat i att nya standarder för tillförlitlighetsprogram har tagits fram där man definierar vilka aktiviteter som krävs för att säkerställa tillförlitligheten och vem som har ansvar för att aktiviteterna utförs.
Den senaste och mest detaljerade standarden är GEIA-STD-0009, Reliability Program Standard for Systems Design, Development, and Manufacturing. Enligt denna standard har beställare och leverantör ett gemensamt ansvar att ta fram ett tillförlitlighetsprogram som säkerställer att beställarens krav och förväntningar uppfylls under produktens hela livslängd. Där definieras vilka aktiviteter som krävs som sedan leverantören är ansvarig för att de utförs, även av underleverantörer.
GEIA har även tagit fram standarder för att säkerställa tillförlitlighet vid implementering av blyfri lödning där man är ännu mer konkret om vad som krävs. I standarderna pekas leverantören av en produkt eller ett system ut som ansvarig för att ta fram en dokumenterad ”lead-free control plan” som beskriver de processer som kommer att användas för att säkerställa att produkten kommer att vara tillförlitlig under den specificerade livslängden. Planen ska beskriva vilka testmetoder som ska användas för att verifiera tillförlitligheten för den aktuella applikationen utgående från förväntade kritiska felmekanismer i den aktuella driftsmiljön med den tänkta konstruktionen.
Fokus i de nya standarderna är att designa in producerbarhet och tillförlitlighet. Detta innebär att designlösningar och komponentval hela tiden måste värderas inte enbart utifrån hur de påverkar funktionalitet utan även utifrån hur de påverkar producerbarhet och tillförlitlighet. Då konstruktörerna inte kan förväntas ha all kunskap som behövs för detta har GEIA-0009 krav på att individer från olika discipliner som design, tillverkning, kvalitet och tillförlitlighet ska vara involverade och samarbeta i alla faser i utvecklingen av en produkt.
De nya standarderna för tillförlitlighetsprogram innebär inte enbart att det krävs ett nytt arbetssätt för att säkerställa tillförlitlighet. De kräver också mycket djupare tillförlitlighetskunnande än vad tidigare arbetssätt har krävt. Det är få svenska företag som har personer med det kunnande som krävs för detta arbetssätt och det är bara ett fåtal personer på dessa företag som har den kunskapen. Det bristande kunnandet om hur man säkerställer tillförlitligheten av elektronikprodukter, men även bristen på resurser för att kunna göra tillförlitlighetstestning, utgör därför ett starkt hot för konkurrenskraften hos svenska företag som tillverkar elektronikprodukter eller har elektronik i sina produkter.
Det innebär en stor risk att överlåta till kund att upptäcka livslängdsproblem. I värsta fall kan det innebära att man har 5–10 års produktion ute i fält när problemen upptäcks och sedan kanske 5–10 års arbete med att komma till rätta med tillförlitlighetsproblemen. Medan det finns omfattande forskning och kunskapsuppbyggande i USA och Asien om hur ny teknik påverkar tillförlitligheten är den nästan obefintlig i Sverige och Europa.
Vi brukar hävda att vår konkurrenskraft bygger på att vi har bättre kompetens än våra konkurrenter. Vad gäller vår förmåga att producera elektronikprodukter och produkter innehållande elektronik med hög tillförlitlighet är det svårt att dra någon annan slutsats än att den är på väg att bli betydligt sämre än i konkurrerande länder, och då främst USA och Asien. Det finns därför ett akut behov av att återuppbygga kompetensen inom det här området i Sverige. Vinnovas SIP-satsning inom elektronikområdet skulle kunna vara en möjlighet för ett kraftsamlande inom området.