Svenskt halvfabrikat bakom kraftkretsar i världsklass
Kistaföretaget Ascatron påstår sig vara bäst i världen på att skapa epitaxi-strukturer för komponenter i kiselkarbid. Hemligheten är en skonsam
tredimensionell dopning. Halvfabrikatet som företaget serverar kan sedan
stoppas in i en vanlig kiselprocess, där kraftkomponenterna tillverkas. ![]() |
Christian Vieider |
![]() |
Adolf Schöner |
Varje kraftkomponent som ska tillverkas, oberoende om det är en switch eller en diod, måste ha sin speciella epitaxistruktur. Den beror av en mängd egenskaper, som spänningen, och kräver olika dopade områden.
– Epitaxistrukturen är det som är mest kiselkarbidspecifikt i konstruktionen och tillverkningen av komponenterna. Inom detta område har vi över 20 års erfarenhet och ingen annan kan göra det vi gör. På epitaxi är vi bäst i världen, säger Adolf Schöner, teknikansvarig på Ascatron.
För att demonstrera sitt material är Ascatron med i flera utvecklingsprojekt där företaget även tar fram komponenter. Däribland ett Eurostarprojekt med mål att ta fram dioder och switchar för 1 200 V och 250 °C samt Vinnovaprogrammet Forska&Väx som ska demonstrera dioder med stabil drift upp till 250 °C och 1 700 V.
– I projekten vill vi visa att vi kan ersätta traditionell jonimplantering med epitaxiella strukturer för att öka prestanda hos de dopade områdena, säger Christian Vieider.
Ascatron grundades hösten 2011 av Adolf Schöner, Christian Vieider, Bo Hammarlund, Sergey Reshanov och Wlodek Kaplan. Företaget – som idag har nio anställda – startade som en avknoppning av en del av forskningsinstitutet Acreos kiselkarbidverksamhet. Från början var tanken att bilda ett kiselkarbidfoundry, sedan dess har affärsmodellen ändrats. Ascatron har precis full-bordat separationen från Acreo, och flyttat två våningar upp i Electrumhuset i Kista. Tillverkningen sker alltjämt i Electrumlabbet. |
Ovanpå en högdopad kiselkarbidskiva lägger företaget, likt alla and-ra, på ett aktivt lågdopat n-skikt med epitaxi. Det utgör själva grundstrukturen. Det är när de dopade strukturerna nära ytan skapas som Ascatron inte följer normen.
– Andra använder jonimplantering, men diffusionen är inte lika hög i kiselkarbid som i kisel så man kan inte driva in dopämnen på samma sätt. Det går inte att nå lika djupt och det skapas lätt defekter när man skjuter in joner med hög energi, förklarar Adolf Schöner.
Defekterna gör att de färdiga komponenterna inte klarar hög spänning och hög temperatur lika bra, samt att livslängden minskar.
– Vi etsar istället ut en struktur och odlar sedan in det p-dopade materialet med epi-taxi. På så sätt kan vi skapa områden med tio gånger så hög dopning som med motsvarande jonimplantering.
Resultatet är, enligt Ascatron, lägre resistans, bättre kontakt till metallen samt färre skador i materialet. Färre defekter ger i sin tur mindre läckström och motstånd, något som minskar värmeutvecklingen och därmed förlusterna när ström körs igenom den färdiga komponenten.
Metoden gör också att det går att skapa betydligt mer avancerade konstruktioner än tidigare, med väldigt djupa och smala dopade områden. Det går även att begrava p-områden i n-material, vilket ger ett lägre fält på komponentens yta. Det minskar läckströmmen, varvid temperaturen kan höjas samtidigt som genombrottsspänningen ökar.
– Inom Vinnovaprogrammet har vi tagit fram de första prototyperna med denna konstruktion. Hittills har vi utvärderat chipen på skivnivå och de klarar 1 700 V. Med en konventionell ytdopad konstruktion hade de i bästa fall klarat 600 V, säger Adolf Schöner.
Samtidigt påpekar han att samma koncept kan användas för switchar och transistorer. Och att det inte krävs speciellt mycket mer för att göra komponenter som klarar betydligt högre spänningar, uppåt 3 300 V eller kanske 5 000 V.
– Vår teknik passar egentligen ännu bättre för högre spänningar. För ju högre spänningen är, desto viktigare är det med materialkvalitet och avancerade konstruktioner som kan hantera negativa effekter, säger Christian Vieider.
De tre mest efterfrågade parametrarna inom industrin är också hög spänning, låg läckström och bra tillförlitlighet.
Men för att komma vidare i utvecklingsarbetet och öka produktionskapaciteten behöver företaget expansionskapital.
– Fortfarande arbetar vi med två single-wafer-maskiner som enbart hanterar en skiva åt gången. I produktion måste vi ha maskiner som kan göra många fler skivor åt gången. Just nu söker vi kapital så att vi kan utöka vår verksamhet, säger Christian Vieider.
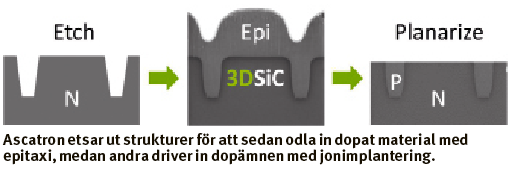