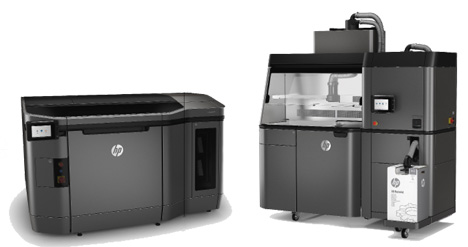
När den amerikanska dator- och skrivarbjässen Hewlett-Packard ger sig in på marknaden för 3D-skrivare ligger ribban högt. Företaget vill bredda tekniken från att vara en arbetsintensiv tillverkningsmetod för prototyper och småserier till att bli en standardteknik i produktionsmiljöer som snurrar dygnet runt och därmed konkurrerar med allt från formsprutning till CNC-fräsar.
Det var hösten 2014 som HP officiellt beslutade sig för att satsa på 3D-skrivare. För att få en snabb start tog företaget in tredjepartsprodukter och satte på den egna loggan samtidigt som man började utveckla en maskin från grunden i ett samarbete mellan företagets enheter i Barcelona och San Diego. I Barcelona finns den största utvecklingsenheten utanför USA med 500 ingenjörer som har ett omfattande kunnande inom den grafiska branschen. Det handlar om storformatsskrivare och digitala tryckpressar som används för att producera allt från fotoböcker och affischer till etiketter på läskflaskor. Kärntekniken – jetprintningen – som skjuter mikrometerstora färgdroppar, kommer från en HP-enhet i San Diego. |
– Jet Fusion 3D är upp till tio gånger snabbare än konkurrenterna samtidigt som kostnaden för utskrifterna är ungefär 50 procent lägre, säger Scott Schiller som är marknadschef för HP:s 3D-skrivare.
Det var strax före sommaren som HP visade upp en prototyp av den nya maskinen som tillverkar plastdetaljer med så kallade voxlar, 3D-världens motsvarighet till pixlar. Voxlarna har en sida på 50 mikrometer. Att bygga med voxlar liknar väldigt mycket att spela Minecraft även om man i 3D-maskinen måste bygga ett helt lager i taget och starta med det understa lagret för att sedan arbeta sig uppåt lager för lager.
Maskinen kan tillverka enstaka delar upp till 30 × 40 × 40 cm eller så kan man tillverka fler mindre delar samtidigt. I och med att det oanvända materialet ligger kvar i varje lager behövs normalt inga stöd, som i andra additiva processer där konstruktionen annars skulle kollapsa under bygget.
Till att börja med finns bara en plast att tillgå, svart nylon. Exakt vad den kommer att kosta vill Scott Schiller inte avslöja men tanken är att leverantörerna ska konkurrera med varandra och därmed driva ner priserna.
Leverantörerna håller på att kvalificera fler plaster med andra färger och egenskaper. Det här kan på sikt användas för att göra komponenterna intelligenta.
– Ett enkelt exempel är att göra de två yttersta lagren i en lyftögla av två avvikande färger, då ser man när komponenten börjar nötas och när det sedan är dags att kassera den, säger Jason DaSilva på HP.
Lite mer avancerat blir det när man adderar plaster som leder elektrisk ström eller ändrar resistans beroende av temperaturen, då skulle det exempelvis gå att bygga in en töjningsgivare eller en Wheatstonebrygga i komponenten så att den kan mäta belastningen eller temperaturen. Självklart kan man också stoppa in konventionell elektronik och ett batteri för att läsa av förändringen och skicka den trådlöst till molnet.
Siemens är en av kunderna som varit med från början och som bland annat ser möjligheter att tillverka reservdelar med maskinen. Det går sällan att ta gamla CAD-data rakt av, eftersom de ursprunglig delarna inte designats för 3D-skrivare. Dessutom öppnar 3D-tekniken möjligheten att designa om delen och kanske göra den lättare eller starkare eftersom 3D-skrivaren har andra möjligheter att bygga upp komponenterna än vad som är möjligt med formsprutning eller fräsning.
Förutom att slippa lagerhållning så gör 3D-skrivaren det möjligt att förbättra funktionen i reservdelen.
– Jag har ett rätt banalt exempel med spårvagnar. Det förekommer att man behöver vika in backspeglarna för att ta sig förbi ett hinder, om man byter ut en del av manöverpanelen som är i plast kan man addera en knapp för att göra det automatiskt, säger Ulli Klenk på Siemens.
I motsats till de flesta andra 3D-maskiner är gränssnittet öppet vilket innebär att användarna kan läsa ut data i realtid. Exempelvis går det att se temperaturen över byggytan under hela tillverkningsprocessen.
– Med de maskiner vi använder idag får vi bara veta att temperaturen varit ok, säger Ulli Klenk.
Exakt vad man ska göra med informationen är inte självklart men den kan exempelvis sparas och plockas fram om en komponenten kommer tillbaka med en reklamation. Den skulle också kunna användas av kunderna för att styra processen enligt speciella önskemål. Och så ger den möjlighet att avbryta tillverkningen om processen av någon anledning spårar ur.
Idag måste man vänta på att allt gått klart och delarna svalnat innan man upptäcker en defekt, en procedur som kan ta upp till fem dagar.
Den kommersiella lanseringen sker sent i höst och maskinen kommer i två modeller, 3200 och 4200. Den senare är 25 procent snabbare och i första hand tänkt för serietillverkning medan den första passar bättre för prototyper.
Självklart tillverkas ungefär hälften av delarna till Jet Fusion 3D av en prototypmaskin.
– Vi gör det inte bara för att vi kan utan för att det blir billigare, säger Scott Schiller.
Priset för den enklare modellen är 130 000 dollar medan den andra går på ungefär 200 000 dollar.
Efterbehandlingsstationen kostar 15 000 dollar.
Lager för lager
|