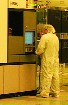
Några siffror om IBM i East Fishkill: * 13 000 kvadratmeter renrum * Målat med 190 000 liter färg * 3 km lång produktionslina * 320 000 km rör och slangar * 1 miljon km kabel och ledning * 900 km Ethernetkabel till maskinerna * Drygt 600 maskiner, snittkostnad 5 miljoner dollar. Dyrast maskin, för kemisk-mekanisk polering (CMP) kostar 90 miljoner dollar. * Linuxbaserat styrsystem med 110 Tbyte lagringsminne och 1,5 Tbyte arbetsminne * Gör 15 000 kiselskivor om 300 mm i månaden. Varje råkiselskiva kostar 1000 dollar * 500 anställda, varav 350 i produktionen * Total investering 3 miljarder dollar |
IBM-fabben i East Fishkill är förvisso stor på många sätt, men jämfört med de största asiatiska fabrikerna är kapaciteten måttlig. Varje månad börjar 15 000 kiselskivor med 300 mm diameter produceras här. Foundryt TSMC i Taiwan har som jämförelse ungefär dubbelt så hög kapacitet.
Styrkan hos IBM är istället flexibiliteten. Medan andra fabbar i världen mestadels jobbar med en eller högst två geometrier, i branschen ofta kallade tekniknoder, så används här fem olika. Serieproduktion görs på 130, 90 och 65 nm, pilotproduktion på 45 nm och utveckling sker på 32 nm-produktion. Även för 22 nm pågår forskning hos IBM, men ingen produktion ännu.
Bara 20 procent för IBMs eget bruk
Ett skäl till flexibiliteten är att bara 20 procent av kapaciteten används för IBMs egna behov, resten är uppdragsverksamhet. Och just förmågan att i högkostnadslandet USA bedriva en produktion som är så konkurrenskraftig och attraktiv för kunderna att den kan bidra till att täcka IBMs egna forsknings- och utvecklingskostnader – det är en del av storheten med denna fabrik.
– Vi har varit lönsamma de senaste åtta kvartalen, berättar platschefen Neil Poullin när Elektroniktidningen kommer på besök.
– Vi var inte först med 300 mm, och vi är inte störst. Men vi har troligen automatiserat mest, och idag används IBMs automationssystem i de flesta 300 mm-fabbar i världen, säger han.
Fabriken körs snudd på helt automatiskt, dygnet runt. Utom 2–3 dagar var fjärde år då alltihop stängs för underhåll. Det hände senast i fjol, fyra år efter 300 mm-premiären 2002. Cirka 90 personer jobbar varje skift, totalt har produktionen 360 anställda.
Neil Poullin kan rada upp imponerande siffror om fabriken. IBM har investerat 3 miljarder dollar här. Renrummet är 13 000 kvadratmeter stort. Produktionslinan är 3 km lång och styrs helt av ett Linuxsystem.
– Vi har mer datorkraft här än Nasa använder för att skicka upp rymdskytteln.
Över 600 maskiner deltar i produktionen, och varje kiselskiva går igenom mellan 500 och 700 steg.
Stordatorernas återkomst ska rädda klimatet IBM gör stora ansträngningar för att positionera sig som ett miljövänligt företag. En miljard dollar om året satsas på utbildning och omorganisation, och 1000 anställda ska blir ”gröna specialister”. Huvudstrategin är att spara ström. Både internt och hos kunderna. IBM, ofta kallat Big Blue, satsar en miljard dollar om året på projektet Big Green. Målet är att inte öka strömförbrukningen trots att datorkraften fördubblas, vilket väntas ske på tre år. – Den mest strömsnåla processorn är den du inte behöver köpa, säger Karl Freund, marknadsstrateg för Big Green. Han berättar att i en datorhall går bara 45 procent av elen åt för att driva datorerna. Mer än hälften går till annat, som luftkonditionering, belysning och liknande. Och av de 45 procenten går bara 30 procent till processorn, resten går till sådant som fläktar, minnen och strömförbrukning. Och av de 30 procent som går till processorn används 80 procent när datorn inte används. – Bara 2,5 procent av den elenergi som matas in i en datorhall används alltså för processorarbete, konstaterar han. Samma sak kan beskrivas i pengar. Räknat som total ägandekostnad (TCO, total cost of ownership) står elenergin för 20 procent av kostnaden för företagsdatorer. Utrustningen, hård- och mjukvara, står för 40 procent medan IT-personal står för 40 procent. – För varje dollar du lägger på en dator måste du alltså betala 50 cent för strömmen, säger Karl Freund. Att få ner strömförbrukningen i enskilda processorer och andra kretsar är i sammanhanget bara en liten del av strategin. Istället gäller det att låta varje processor, och varje dator, utföra mer nyttigt arbete. Här kommer IBMs stordatorer in, och företagets förmåga att virtualisera processer i dessa datorer. – Med våra stordatorer och optimal virtualisering kan vi nå en utnyttjandegrad över 90 procent. En unixserver utnyttjas som jämförelse bara till 15 procent, och en Windowsserver 7 procent, säger säger David Anderson, som har titeln ”grön trollkarl” – Green Wizard – på sitt visitkort. Stordatorer förknippas normalt inte med energisnålhet, men det menar Anderson är orättvist nuförtiden. – De senaste 15 åren har vi gjort dem 14 gånger effektivare, mätt som Mips/kW. Vår System Z drar 75 W, har dubbla processorkärnor och kan hantera 30-60 virtualiserade processer per kärna. Jämfört med serverfarmer sparar System Z 80 procent av energin och därtill 85 procent av golvytan, säger han. |
– Bara hälften är för produktion. Resten är för mätning, styrning och kvalitetskontroll. Varje maskin stoppar automatiskt om något är onormalt – det räcker med att mätdata hamnar utanför gränsvärdena.
350 olika typer av kretsar
Totalt finns i fabben 1,5 miljoner processrecept som vart och ett kan ha 100 processteg plus lika många mät- och styrsteg. Varje sådant steg kan omfatta 250 parametrar. Omkring 350 olika möjliga processflöden kan resultera i lika många typer av kretsar. Utifrån identiska kiselskivor kan slutresultatet exempelvis bli kisel på isolator, lågeffektkretsar, något med inbäddade passiva komponenter, processorer med inbyggt DRAM eller med analoga delar.
Varje skiva tar 75–85 dagar att producera. Tiden har hållits konstant sedan 0,25 µm-produktionens dagar trots att antalet masklager ökat för varje generation. Vid 65 nm används oftast omkring 50 masklager, en siffra som väntas öka till 60 för 45 nm. Och varje lager tar 1,3 till 1,5 dygn i snitt.
– Vi kan pressa den tiden till 0,8 dagar för högprioriterade wafers, vissa kunder kräver det och är villiga att betala för det, säger Neil Poullin.
Å andra sidan har IBM lyckats minska ställtiderna och väntetiderna mellan verktygen för varje generation. Framför allt genom att minimera tiden mellan verktygen. Av de 75–85 dagarna tillbringar kiselskivan bara 25–30 dagar i någon av maskinerna. Resten är väntetid – i genomsnitt tar det 8 minuter mellan varje verktyg.
– Men i 45 nm-produktionen har vi pressat det till 3 minuter.
Det är inte helt lätt att förstå hur små geometrier detta handlar om, men renrumsklassificeringen ger en antydan. Varje maskin är ett eget litet renrum av klass 1, den högsta som finns standardiserad, och kiselskivorna flyttas mellan maskinerna i hermetiskt slutna kapslar som också håller renrumsklass 1. Ettan betyder att det får finnas högst en partikel större än 500 nm per kubikfot. Men samtidigt får det finnas 35 partiklar större än 100 nm. Och för mindre partiklar finns ingen standard. Ändå fungerar produktionen vid 45 nm.
Rymddräkterna behövs inte
Renhetskraven i maskinerna och transportkapslarna gör att de övriga renrumskraven egentligen inte är så höga – de håller klass 100. Det är faktiskt inte av renhetskrav som personalen i fabriken bär de karaktäristiska heltäckande dräkterna.
– Vi skulle kunna ta bort skyddskläderna. De bidrar marginellt till renheten. Men kunder och partner vill att vi behåller dem.
Jämfört med många andra halvledartillverkare håller IBM en mycket öppen attityd. Besökare är välkomna till fabriken – här guidas journalister och analytiker, skolbarn och studenter, politiker, lobbyister och förstås kunder tre-fyra gånger i veckan. Vi släpps inte in i renrummet, men får fotografera fritt genom fönstren. Och även för produktionsdata är IBM ganska givmilt.
– Den viktigaste siffran för oss är andelen ”first time right”, alltså hur många skivor som ger kretsar som fungerar på första försöket. Vi brukar ligga kring 97 procent i snitt, men de senaste två kvartalen har vi varit hundraprocentiga, berättar Neil Poullin och ser påtagligt stolt ut.
Hur är det då med processutfallet, yielden, det i halvledarproduktionssammanhang heligaste av alla tal som visar hur stor andel av de producerade kretsarna som faktiskt fungerar som tänkt? Den siffran ger ingen halvledartillverkare ifrån sig frivilligt, och här tar även IBMs öppenhet slut.
– Siffran är förstås inte officiell. Men jag kan säga att på den första skivan i en produktion kan den ligga så lågt som 35 procent, och det tar omkring en vecka att nå 50 procent. Så småningom når vi tillräckligt högt för att vara konkurrenskraftiga.
– Och det kisel som inte fungerar säljer vi till en partner som gör solpaneler av det, berättar Neil Poullin.