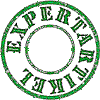
![]() Fler tekniska rapporter finns på etn.se/expert |
I projektet testades bland annat livslängden för ett antal komponenttyper som är benägna att få utmattningsbrott i lödfogarna. De testade komponenterna var BGA208, BGA256, BGA676, QFN48, QFN72 samt keramiska motstånd (1206 och 2512). BGA208 hade 0,8 mm pitch medan de två andra BGA:erna hade 1,0 mm pitch.
Temperaturcyklingen gjordes mellan –40 och 125 °C med en temperaturändringshastighet på 5 °C/min, 10 minuters hålltid vid –40 och 20 min vid 125 °C. Det bör dock påpekas att även andra felmekanismer kan påverkas av blyfri lödning som till exempel sprödbrott i lödfogar och bildning av CAF (coductive anodic filament).
Resultaten från temperaturcyklingen visas i figur 1 och i tabellen presenteras de som karakteristisk livslängd vilket anger det antal cykler då 63,2 procent har fallerat. Intressant att notera är att livslängden för BGA:erna var längre för de blyfria komponenterna medan övriga blyfria komponenter har kortare livslängd. Detta är i överensstämmelse med vad många andra har rapporterat och beror på vilken krypning lödfogarna utsätts för. För komponenter med låg stand-off, som QFN och keramiska motstånd, utsätts lödfogarna för hög krypning vilket har mest negativ inverkan för blyfria lödfogar.
Det finns ingen standard som har specificerade krav på antalet cykler som fordonselektronik bör klara men IPC-9701 har för ett antal produktkategorier definierat vilka temperaturcykler produkterna kan tänkas utsättas för liksom maximalt antal tillåtna fel, bland annat för fordonskupé. En omräkning till vad det skulle motsvara vid ett temperaturcyklingstest ger att den karakteristiska livslängden bör vara minst 1 500 cykler för 10 års livslängd och 2 250 för 15 års livslängd.
Det vill säga, BGA208 lött med tenn/bly och CR2512 lött med blyfritt klarade inte ens kravet för 10 års livslängd i kupé medan CR2512 lött med tenn/bly nätt och jämnt klarade kravet. BGA208 lött med blyfritt klarade kravet men med liten marginal. Det bör dock påpekas att IPC:s data är framtaget på nittiotalet och för tenn/bly-lod så relevansen kan ifrågasättas, speciellt för blyfritt.
Det är oroande att BGA208 med tenn/bly inte ens klarade kravet för 10 års livslängd i kupé. Det kan då kännas uppmuntrande att blyfritt klarade kravet om än med liten marginal, men mikrosektioneringar av lödfogar till de olika komponenterna visade att läget är än sämre än vad siffrorna visar och speciellt för blyfritt.
Mikrosektioneringarna visade sprickor i mönsterkortslaminatet. Dessa fanns under och vid lödpaddar för alla BGA:er men mest för den blyfria BGA208 (se figur 2). En effekt av sprickorna är att belastningen minskar på lödfogarna vid temperaturcyklingen. Detta resulterar i en förlängd livslängd av lödfogarna, vilket man kan se som positivt. Det finns dock risk för att sprickorna orsakar andra fel som avbrott i anslutande ledare eller att fukt och föroreningar tränger in i laminatet.
Vid en temperaturcykling mellan –40 och 75 °C uppstod inga sprickor i laminatet. Det är därför inte troligt att sprickorna skulle uppstå i kupémiljö. Detta innebär att om man försöker omräkna resultaten från testningen mellan –40 och 125 °C till kupémiljö kommer man kraftigt överskatta livslängden och mest för blyfritt. Det finns därför en betydande risk för att kretskort med BGA:er inte kommer att ha förväntad livslängd ens i hytt/kupé-miljö, än mindre i strängare miljöer. Detta gäller även för QFN:er. Det finns flera skäl till detta där det blyfria lodet i sig inte är den viktigaste orsaken.
Ny ingjutningsplast
För att klara MSL3-klassning vid blyfri lödning har man bytt ingjutningsplast för halvledarkomponenter. Den nya plasten består av MAR (polyaromatic resin) och har hög halt av oorganiska fyllmedel för att minska fuktupptaget. Detta medför att CTE för plasten har minskat till 7–9 ppm/°C. Som jämförelse har alumina som används för tillverkning av keramiska komponenter ett CTE på 8,1 ppm/°C. För benlösa komponenter, som ytmonterade passiva komponenter, QFN- och BGA-komponenter monterade på FR4-kort medför detta en kraftigt ökad belastning på lödfogarna vid temperaturförändringar.
Simuleringar utförda av det belgiska forskningsinstitutet Imec har visat att livslängden av lödfogar till QFN- och BGA-komponenter kan minska med upp till 85 procent. De flesta halvledarkomponenter har denna ingjutningsplast idag, även de komponenter som tillverkas för lödning med tenn/bly-lod. Detta innebär att för kort som fortfarande löds med tenn/bly-lod kan livslängden ha minskat med 85 procent utan att man är medveten om detta. Därav det dåliga resultatet för BGA208 med tenn/bly-lod.
När komponenttillverkarna bytte plast skickade de ut PCN:er (product change notification) där man angav att förändringen inte påverkade tillförlitligheten av komponenten. Strikt hållet är detta sant att eftersom de bara testar lösa komponenter och inte tillförlitligheten av lödfogar till komponenterna. Få köpare är nog medvetna om detta utan tolkar troligen PCN:erna som att förändringen inte heller påverkar lödfogarnas tillförlitlighet.
Vid testningen i FFI-projektet utfördes temperaturcykling mellan –40 och 125 °C. Resultaten visade att de resulterande höga belastningarna på lödfogarna på grund av den nya plasten även kan orsaka att sprickor bildas i mönsterkortslaminatet. Eftersom blyfria lod är mindre elastiska än tenn/bly-lod ökar risken för sprickor i mönsterkortet med blyfria lod. Sprickorna i mönsterkorten var därför fler och större för de blyfria BGA:erna.
Även de mönsterkortslaminat som tagits fram för blyfri lödning ökar troligen också risken för sprickor eftersom de är sprödare. IPC:s standarder för lödda kretskort har inga acceptanskrav för denna typ av sprickor så det är upp till var och en att bedöma vad som är acceptabelt.
Chipstorlek
För QFN- och BGA-komponenter med stort chip i förhållande till komponentstorleken (chip-size komponenter) begränsar chipet komponentens CTE i ännu högre grad än ingjutningsplasten. För dessa komponenter sker därför en ännu större minskning av lödfogarnas livslängd när de är placerade under eller nära chipkanten. BGA208-komponenten som testades i projektet hade ett chip som var 11 5 11 mm. Det var därför troligen en kombination av stort chip och ny plast som gav det dåliga resultatet.
För att förbättra livslängden har man försökt undvika att ha lödfogar under chipet för BGA:er som används i fordonsapplikationer. För vissa typer av BGA:er, som t ex SuperBGA, är det till och med omöjligt att placera lödfogarna under chipet. Nackdelen är att dessa komponenter är mer utrymmeskrävande och har sämre elektrisk prestanda. Det är därför allt färre komponenttillverkare som tillverkar dem.
Även om QFNer inte har lödfogar placerade under chipet så har chipets storlek stor påverkan på lödfogarnas livslängd. Om kvoten mellan chip- och komponentstorleken ökas från 0,5 till 0,8 minskar lödfogarnas livslängd med 50 till 80 procent. Om QFN-komponenten har två eller fler små chip blir effekten liknande eftersom chipkanterna kommer nära kapselns kanter.
Pitch
Vid minskande pitch för BGA:er minskar livslängden för lödfogarna. Vid pitch på 0,8 mm eller mindre kan livslängden bli ett problem även i hytt/kupé-miljö beroende på chip- och komponentstorlek. För pitch på 0,5 mm eller mindre kan tillförlitligheten bli ett problem också för produkter med betydligt kortare förväntad livslängd även för relativt små komponenter. I dessa fall krävs att man applicerar underfill under komponenterna för att förbättra livslängden på lödfogarna. Det är dock en kostsam process som man helst vill undvika och det är därför viktigt att man har kunskap att kunna bedöma när det krävs underfill.
Vätning av lödytor på QFN
QFN:er har i allmänhet lödytor som är exponerade både under och på sidorna av komponenten men det är bara på undersidan som lödytorna har en skyddande plätering, i allmänhet Sn eller Ni/Pd/Au. På sidorna är kopparn exponerad och oxideras lätt. Lödbarheten på sidorna sjunker därför snabbt vid lagring vilket resulterar i sämre uppvätning på sidorna men också i att komponenten kan komma att sitta snett i höjdled. Detta är ett större problem vid blyfri lödning eftersom vätningen är sämre med blyfria lod (se figur 3). Resultaten från projektet visade att detta kan minska livslängden med 70 procent. Trots detta så har IPC:s standarder för lödda kretskort inga krav på vätning på sidorna av QFN:er.
Skyddslack
I projektet var testkorten inte lackade men resultat från testning av lackade kort (både publicerade och icke publicerade resultat) har visat att lackning av QFN- och fine-pitch BGA-komponenter kan minska livslängden med upp till 85 procent. För att undersöka detta har testning utförts efter projektets avslutning där ett lackat testkort med QFN38-komponenter (inga BGA:er) temperaturcyklades. Temperaturcyklingen utfördes mellan –40 och 85 °C. Lödfogarna till QFN38-komponenterna fallerade efter 500 till 600 cykler. QFN-komponenterna hade dålig vätning på sidorna så det tidiga felutfallet var nog en kombination av den dåliga vätningen och effekten av lackning. För att klara kravet på 10 års livslängd i hyttmiljö enligt IPC borde de klarat åtminstone 3 000 cykler.
Dessutom, eftersom komponenten var så pass liten och den dessutom hade ett relativt litet chip, borde den ha klarat betydligt mer än 5 000 cykler på ett olackat kort. Kombinationen dålig vätning och lackning har därför troligen minskat livslängden av lödfogarna med minst 90 procent.
Relevansen av testning enligt ISO 16750
Fordonstillverkare har ofta krav på alla elektronikenheter ska kvalificeras enligt ISO 16750 om än med modifieringar. En del av projektet var därför att utvärdera om dessa test är relevanta för att upptäcka tillförlitlighetsproblem orsakade av blyfri lödning. Testningen enligt dessa test indikerade inga tillförlitlighetsproblem så uppenbarligen är dessa test inte relevanta för att utvärdera tillförlitligheten av blyfri kretskort. Detta påpekas för övrigt i inledningen av standarden även om man uttrycker sig lite vagt;”ISO 16750 does not necessarily ensure that environmental and reliability requirements for solder joints, solderless connections, integrated circuits, and so on are met”.
I stället bör tillförlitligheten av dessa säkerställas på material-, komponent- eller kretskortsnivå. Problemet är att någon sådan testning inte utförs under framtagning av en elektronikenhet. Projektet väcker därför frågan vilket ansvar de olika parterna i produktframtagningskedjan har för slutproduktens tillförlitlighet.
Detta kommer att diskuteras i en senare artikel.