
Och visst låter en metod som kan halvera tillverkningskostnaden för traditionella mönsterkort samtidigt som den ger bättre högfrekvensegenskaper, fungerar på substrat som plast, glas och papper, är miljövänlig och som grädde på moset dessutom passar in i det befintliga ekosystemet för bra för att vara sann.
Han började som vd på Cuptronic för två år sedan i samband med att han hjälpte några privata investerare med att göra en genomgång (due diligence) av företaget. Bland annat kontaktade han då Tyco och Cisco men även stora mönsterkortstillverkare för att undersöka deras intresse av Cuptronics process.
Slutanvändarna var dock inte i första hand intresserade av den besparing på upp till 50 procent av kostnaden för tillverkning av mönsterkort som Cuptronics process lovar att ge. Utan mer av de förbättrade högfrekvensegenskaperna som man får genom att det är möjligt att göra smalare ledare med rakare kanter.
– Idag klarar man att göra mönsterkort med ledare på 75 mikrometer, kanske något mindre, men då har man en kassation (i Asien) på mellan 40 och 50 procent. Vi har gjort 48 mikrometer i en konventionell process och har i princip ingen kassation.
Men hur smala ledarna kan göras bestäms egentligen av litografin.
– Vi borde kunna göra ledare som bara är ett par mikrometer breda, säger Peter Sjöbeck.
På de dimensionerna finns ett annat svenskt innovationsföretag, Replisaurus, som håller på att utveckla en process för att lägga ledare på halvledarkretsar. Men företagens tekniker är tekniskt olika.
Snart i kommersiell användning
Cuptronics tillverkningsmetod är klar för lansering. Under första halvan av nästa år kan de första mönsterkorten tillverkade med tekniken finnas på marknaden. Var eller vem det blir är inte klart, det pågår förhandlingar med både amerikanska och asiatiska företag.
Men vägen till en kommersiell produkt har inte direkt varit spikrak. Cuptronic grundades redan 1996 av Karl Gunnar Larsson.
– De kom på metoden genom trial and error och fick hjälp av den dåvarande KTH-professorn Bengt Rånby.
Cuptronic siktar egentligen på en rent additiv process men i dagsläget är den fortfarande semiadditiv, vilket innebär att man börjar med att belägga hela mönsterkortet med kopparskikt som är 3 mikrometer tjockt. Det kan jämföras med dagens kommersiella processer där man utgår från laminat som har ett kopparskikt med en tjocklek på 18 till 20 mikrometer.
Med Cuptronics metod fortsätter man sedan på samma sätt som i en konventionell mönsterkortsprocess. Man mönstrar med torrfilm för att markera var ledarbanorna ska vara, bygger upp ledarbanorna (pläterar) till önskad tjocklek (normalt 30 mikrometer), tar bort torrfilmen (strippar) och etsar ner kopparn 3 mikrometer så att ledarbanorna friläggs.
Kortare etstid ger raka kanter
Eftersom baskopparskiktet är betydligt tunnare i Cuptronics process blir underetsningen på ledarna minimal. De kan därför göras smalare och får rakare kanter än i en konventionell process där man måste ha betydligt längre etstider.
– Det går visserligen att köpa konventionella substrat med 3 mikrometers kopparskikt men de är extremt dyra. Ett annat alternativ som en del mönsterkortstillverkare använder är att köpa laminat med 18 mikrometer koppar och sedan etsa ner det till fem mikrometer innan man börjar sin tillverkning, säger Bengt Källbäck som tidigare var vd på Cuptronic men som idag driver företaget HLB Catheter (se separat ruta).
Cuptronics process fungerar bäst på halogenfria material men med en primer går det att använda i stort sett vilken bärare som helst. Förutom vanliga FR4-kort kan man använda teflon, papper, glas, ABS-plast eller Topas. Det senare är en plast som har lägre dielektricitetskonstant än teflon och därför är intressant för högfrekvenstillämpningar.
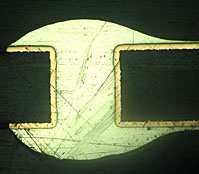
Processen kan förbättras
Målet för Cuptronic är dock att få fram en rent additiv process där man alltså inte behöver ta bort någon koppar. Processen fungerar i labbet men behöver kommersialiseras. Det finns flera olika lösningar som man bollar med. Bland annat skulle man kunna speja på polymerlösningen och sedan rita med en laser på de ställen där man vill ha ledare. En annan möjlighet är att använda en bläckstråleskrivare för att lägga på polymerlösningen.
Båda metoderna öppnar för att göra sant tredimensionella mönsterkort.
– Volvo har bett oss provat att belägga höljet till kupébelysning till nya V70:n som är av ABS-plast med ledarbanor för att ersätta det råttbo som finns där idag.
Men prioritet ett är trots allt att få ut den semiadditiva processen på marknaden.
– Fördelen med vår process är att det går att ställa in en maskin som är fem meter lång och som kostar kanske fem miljoner kronor parallellt med en befintlig produktionslina.
– Man kan börja med att köra några paneler för att prova, sedan rampa upp tills man känner sig säker för att slutligen ersätta dagens teknik, säger Peter Sjöbeck.
Han är övertygad om att det inte finns några problem med tillförlitligheten.
– Redan för tre år sedan tillverkades ett antal kort för medicinsk utrustning som testades utan tecken på att de degraderade.
Frågan är då varför ingen annan har lyckats med det här?
– Det beror på hur vi sätter fast polymersträngarna på ytan. Normalt brukar man tillverka strängarna först och sedan sätta fast dem. Vi gör tvärtom. Utgår från monomerer och låter polymersträngarna växa från ytan och uppåt. De binds med kovalenta bindningar till substratet och blir därmed mycket svårt att dra loss mekaniskt, säger Peter Sjöbeck.
Kateter tillverkad med Cuptronics process Skapaprisvinnaren HLB Catheter i Täby är ett nystartat företag som baserar sin produkt på flexibla mönsterkort. Speciellt fördelaktigt är det att använda Cuptronics metod som ger mycket smala ledare på tunna laminat. HLB Catheter håller på att utveckla en kateter som ska användas för att ställa diagnos på patienter med hjärtproblem. Katetern förs upp genom ljumsken in till hjärtats vänstra kammare för att mäta tryck och volym på hjärtat. Företaget vann Skapapriset på 300 000 kronor i fjol och fick 900 000 kronor av Vinnova i våras för att verifiera tekniken. Dessutom har Sting Capital gått in med en miljon kronor i såddfinansiering. Den kateter företaget utvecklat är i själva verket ett tunt och halvmeterlångt mönsterkort med en mikromekanisk sensor i ena ändan och kontakter i den andra. Själva katetern får man genom att dra det långsmala mönsterkortet genom vad som kan liknas vid en tratt så att det rullas ihop samtidigt som det förseglas med lim. Förutom att metoden måste vara billig ska mönsterkortet tåla att böjas en miljon gånger eftersom mätningen av hjärtat kan pågå i flera dagar. Fotnot: Kateter är ett rörformat medicinskt instrument, numera vanligtvis av plast, som är avsett att stickas in i kroppen för att tömma ut vätska, för att införa läkemedel eller göra diagnostiska mätningar. |
Ger bättre vidhäftning
Istället för att få ”garnnystan” med polymersträngar som fäster vid ytan får man då något som liknar en ryamatta och som har 40 procent fler fästpunkter. Ovanpå polymerskiktet fäster man sedan Palladium-komplex som reduceras till metalliskt Palladium för att det ska gå att fälla ut koppar katalytiskt.
– Vi har haft en fungerande metod i över två år men uppfinnaren, KG Larsson, att det skulle fungera på alla laminattillverkarnas material och så ville vi veta exakt hur och varför metoden fungerade. Vi har fått hjälp av professor Anders Hult på KTH med det, säger Peter Sjöbeck.
Metoden är skyddad av godkända patent i USA och Europa. Däremot inte i Asien.
– Det är inget problem eftersom man inte kan sälja produkter i Europa eller USA som tillverkats i Asien och som bryter våra patent.
Mycket mjuka pengar
Cuptronic har under årens lopp finansierats av grundarna och av ”mjuka pengar” från olika forskningsfinansiärer som Vinnova, Teknikbrostiftelsen, Nutek, Länsstyrelsen, Norrbottens forskningsråd, Längmanska fonden och Kalix kommun där KG Larsson bor. De senare har inte gått direkt till företaget utan betalat arbete som utförts på Umeå universitet, Luleå tekniska högskola och på KTH.
– Jag bedömer att privata finansiärer är enda sättet att slutfinansiera sådana här bolag där det finns intressant teknik men också vissa risker, säger Bengt Källbäck.
– Vi har fått fyra miljoner sedan jag kom in och är garanterade ytterligare två om det behövs så finansieringen är inget problem, säger Peter Sjöbeck.
– Finansiärerna ser mönsterkortsdelen som mycket intressant. Men minst lika stor potential finns i solceller och bränsleceller där vår metod kan göra produktionen betydligt billigare.