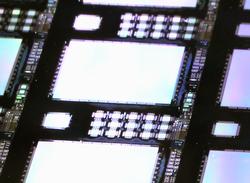
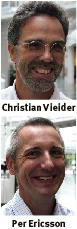
Acreo har utvecklat infraröda sensorer under många år. För tre år sedan knoppade forskningsinstitutet av sin verksamhet kring avancerade kylda sensorer i företaget Irnova. Kvar blev utvecklingen av enklare okylda ir-sensorer, som nu med god hjälp från Autoliv och Sensonor kommit dit att en kommersialisering finns inom räckhåll.
– Autoliv har haft en väldigt drivande och central roll för att vi kommit så långt som vi nu gjort i Sverige med denna teknik, säger Christian Vieider.
Han menar även att Autolivs långvariga samarbete med norska Sensonor är på väg att skapa helt nya spelregler inom ir-världen. Traditionella bolometeraktörer är amerikanska företag, nästan alltid med någon form av försvarskoppling. Hittills har det hängt på de amerikanska exportreglerna, vilken teknik som får användas av en billtillverkare som vill sälja sina bilar världen över.
– Sedan i fjol har vi ett avtal med Sensonor som innebär att vi tillsammans ska skapa en kommersiellt realiserbar ir-sensor. Det är uppryckande för marknaden att det kommer in en helt ny aktör som är van att sälja till bilindustrin och inte till militären. Sensonor har ett helt annat volymtänkande och andra kvalitetsnormer, säger Per Ericsson, projektledare på Acreo.
I utvecklingsarbetet är det själva sensormatrisen som Acreo ansvarar för. Arbetet sker i tajt samarbete med KTH, som är specialiserat på den mikromekaniska delen. Och pengarna kommer bland annat från EU.
Utläsningskretsen har EU där-emot inte bidragit till – trots att kretsen är ett måste för att sensorn ska kunna utvärderas och sedan användas. Den har istället utvecklats i två parallella projekt – ett med Autoliv, Vinnova och FMV och ett med Sensonor och partners.
– Kretsen är konstruerad. Just nu väntar vi på att få wafers från foundriet så att vi kan tillverka sensorerna, säger Per Ericsson.
Nästa steg i projektet är alltså att kombinera utläsningsdelen med de sensorelement som utvecklats i labbet i Electrum i Kista. I labbet har uppgiften varit att ta fram en så känslig och samtidigt så billig sensormatris som möjligt.
Bildsensorna skapas i Electrum Bildsensorerna som Acreo är med och utvecklar med bland andra Autoliv, Sensornor och KTH byggs av två olika wafers. Den ena är tillverkad av Acreo i Kista och utgör basen för själva bildsensorn. Den andra är en CMOS-skiva, tillverkad hos ett foundry, späckad med utläsningskretsar. När de två skivorna bondats samman etsas den mikromekaniska strukturen fram i labbet i Electrum. Resultatet är CMOS-skiva på vilken en stor mängd bildsensorer vuxit fram. Varje pixel består av ett membran som hålls upp av tunna ben direkt ovanför en utläsningskrets. Benen används för att leda ut den elektriska signalen från respektive bildelement, men de får inte leda värme. Ovanpå detta bondas ytterligare en etsad kiselskiva som gör att varje sensormatris omges med vakuum. Först därefter skärs wafern upp i chips. Acreo finns med i en mängd olika projekt som rör okylda ir-sensorer – bland annat samverkar forskningsinstitutet med Daimler och Umicore, förutom Autoliv, Sensonor och KTH i EU-projekten ICU och FNIR, samt driver excellens-centret Imagic. |
Lägger man då till att en kamera ska kunna fungera från –45 °C till +90 °C, trots att sen-sorn varken är kyld och stabiliserad, inser man att utmaningen är tuff.
– Vi mäter alltså mycket små temperaturskillnader på långt avstånd med en temperaturgivare som i sig flyter i temperaturen.
Varje bildelement består av ett tunt membran som hålls upphängd med tunna smala ben ovanför ytan av en utläsningskrets (se faktaruta).
Temperaturförändringen i membranet omvandlas till en elektrisk signal med hjälp av en termistor – en temperaturkänslig resistans – som är integrerad i membranet.
– Det är en av de delar som vi på Acreo har jobbat allra hårdast med. Vi har brottats med hur man gör en sådan väldigt känslig och utan att tillföra eget brus.
En väsentlig del i framgången är materialvalet. Skivan som utgör basmaterialet för membranen består av enkristallina flerlagersstrukturer av kisel och kiselgermanium. Funktionen förklaras med de olika bandgapen hos Si- och SiGe-lagren, och hur de påverkar hålens färd genom membranet. Den enkristallina strukturen ger i sin tur mycket lågt brus, vilket bäddar för hög känslighet och hög noggrannhet.
– Kring detta har vi tagit fram patent. Tekniken bottnar egentligen i tidigare utveckling där vi använt galliumarsenid. Men nu har vi jobbat intensivt med att föra över tekniken till kisel. Det gör det mycket billigare, säger Christian Vieider.
Försöken att skapa billigare lösningar lyser igenom i hela projektet. I varje detalj tittar man på vad som kostar, och om det går att göra lösningen billigare. Ett exempel är att man försöker ändra formen på benen som håller upp membranet, så att de inte tar onödig plats. Ett annat är kapslingen.
– Idag kapslar tillverkarna chipsen ett och ett. Vi hanterar hela skivor istället och kapslar på wafernivå. Först efter kapslingen delar vi upp skivorna.
Resultatet är en färdig krets på cirka 12 5 12 mm, där sensormatrisen är 8 5 6 mm. Det är alltså basen i en nattkamera i morgondagens bil och motsvarar i stort bildsensorn som sitter i en mobiltelefon eller systemkamera.
– Men sensormatrisen och utläsningskretsen kan också användas i en kamera som används för att mäta temperatur. Tillämpningen är ett senare steg i signalbehandlingen. Skillnaden i systemen ligger också på ett annat plan, exempelvis på hur väl man kalibrerar chipet och hur väl man temperaturstabiliserar det, säger Per Ericsson.
På sikt finns det tankar om att ta ytterligare ett steg i krympningsprocessen genom att bygga in linsen som en del av chipset – idag är de separata enheter.
Pixelstorleken är också något det talas om att minska. Idag är 25 µm en sorts standard, men en mindre pixel bäddar för mind-re chips eller chips med högre upplösning på samma yta.
– Men jag tror inte att det är meningsfullt att göra pixlar som är mindre än 12 µm, då hamnar man nära diffraktiongränsen eftersom ljuset som ska fångas in har en våglängd på cirka 10 µm, säger Per Ericsson.