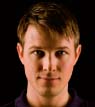
Istället försöker Replisaurus sälja in tekniken med argumentet att ledarna blir exakt som man ritat dem utan rundade kanter och ojämn bredd eller höjd. Det ger en designfördel eftersom repeterbarheten, de små dimensionerna, de raka kanterna och den jämna höjden gör att processen kan användas för att tillverka mer exakta spolar och kondensatorer i det översta ledarlagret. När de passiva komponenter flyttas in på chippet får man betydligt bättre rf-kretsar.
PATRIK MÖLLER Befattning: VD Replisaurus AB, VP Technology Replisaurus Inc. Född: 1977 Bor: Kungsholmen Familj: Flickvän Karriär: Kemiingenjör från LTH/UC Berkeley. Uppfinnare av ECPR-tekniken. Grundare av Replisaurus tillsammans med Mikael Fredenberg och Peter Wiwen-Nilsson. Industridoktorand på KTH. Intressen: Squash och skidåkning. Bra Espresso. |
Det som gör Replisaurus unikt jämfört med andra företag som sysslar med replikering är att man både gör litografin och själva metalliseringen i ett enda elektrokemiskt printsteg. Det fungerar eftersom maskinen arbetar som en tryckpress där mastern utgör en stämpel som fyllts med den kopparbaserade elektrolyt som ska bilda ledarmönstret. Men det räcker inte med att bara trycka mastern mot ytan för att få ett mönster.
För att kopparlösningen ska ”fastna” måste underlaget, det vill säga wafern med integrerade kretsar, först ha försetts med ett tunt groddskikt av just koppar. Sedan trycker man med mastern vars hålrum fyllts på med kopparlösning och applicerar en ström för att få igång processen. När den är klar etsas groddskiktet bort.
Gör folk tokiga
Resultatet blir ett ledarmönster med extremt bra egenskaper.
– Vi kan göra ledare som är 10 µm tjocka och 5 µm breda eller 500 nm tjocka och 500 nm bredan med samma maskin. Det enda man byter är mastern.
Patrik Möller visar en SEM-bild på datorn som ser ut att vara ritad, så raka är kanterna. Sen bläddrar han fram en bild som visar två parallella ledare med 10 µm bredd och där avståndet mellan ledarna är 5 µm.
– När vi är ute och pratar med tillverkare är det sådana här bilder som gör folk helt tokiga, säger han och ler.
Noggrannheten i Replisaurus teknik påverkas inte heller av hur mönstret ser ut, hur breda ledarna är eller hur tätt de placeras vilket är fallet med alternativa metoder.
– Idag måste man designa efter processens regler som sätter begränsningar för vad man kan göra men med vår teknik får du samma sak på din wafer som du ritar i cadden.
Dessutom blir det exakt likadant från chip till chip. I alla fall på de 500 första kopiorna från mastern. Sedan är den utsliten och kasseras.
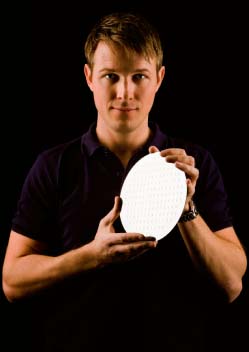
Själva mastern tillverkas av en kiselskiva som är lika stor som den wafer som ska processas. Replisaurus arbetar med åttatumsskivor idag men har också tittat på 12 tumsskivor som kan bli nästa steg.
Wafern processas med konventionell litografi för att skapa det önskade mönstret. Idag sker det i den del av renrummet i Electrum som Replisaurus hyr samt hos mindre forskningsfoundries. Men för att klara kraven från framtida kunder är planen att använda ett kommersiellt foundry.
– Vi håller på att utvärdera olika tänkbara partners.
Det handlar både om att säkra leveranserna men också om att få ner ledtiderna så att de blir i samma storleksordning som för tillverkning av fotomasker.
– Sen kan man tänka sig att de största kretstillverkarna vill göra mastrarna i egen regi precis som de tillverkar fotomaskerna själva.
Den ursprungliga tanken när Replisaurus startade var att använda replikeringen för att sänka tillverkningskostnaden för halvledartillverkarnan. Det är fortfarande en del av affärsplanen men fokus har svängt under resans gång och idag ser Patrik Möller tre huvudområden för tekniken.
Bättre rf-kretsar viktigaste argumentet
Som nämnts vill man sälja in den som en designfördel när det gäller att konstruera rf-kretsar. Idag använder bland annat Nokia en metod med att flip-chipmontera passiva komponenter på ett glassubstrat ovanpå rf-chippet. Den hybridlösningen vill Replisaurus ersätta med integrerade passiver i det översta ledarlagret.
En annan fördel är att tekniken kan användas för att tillverka kopparpelare, även kallade mikrobumpar, på integrerade kretsar. Det är små kopparpelare som används för att ersätta lodkulorna när man ska flip-chipmontera kretsar som till exempel processorer. Tekniken blir billigare eftersom man slipper nickel och guld som idag används som ytbeläggningar.
När väl Replisaurus teknik är etablerad kan den också börja konkurrera hos halvledartillverkare och kapslingshus som gör annat än rf-kretsar eller processorer. Bland tillämpningarna finns så kallad redistribution, en teknik där det översta ledarlagret används för att få anslutningarna på precis den plats man önskar. Redistribution används bland annat vid flip-chipmontering och vid stackning av okapslade kretsar.
Många vill samarbeta
I Replisaurus tappning kan åtta processteg ersättas med tre.
– Vi jobbar med en av de fem största halvledarföretagen i ett gemensamt utvecklingsprojekt där vi testar deras designer i vår process. Vi jobbar också med ett av de ledande företagen inom integrerade passiver.
I kön av intressenter finns också foundries.
– Många vill bli först med en sådan här process som gör att de kan särskilja sig. Men vi försöker också sälja in tekniken till fabrikslösa företag. De har hela arméer av processingenjörer som sitter och designar ihop med foundries.
Tanken är att försöker skapa en efterfrågan så att foundryna ska våga satsa.
En hake med ny tekniken brukar vara att designverktygen inte klarar att leverera vad produkten i sig kan leverera. Men enligt Patrik Möller är det inget problem i det här fallet.
– Det handlar egentligen bara om att ta bort de nedgraderingar de har idag för att kompensera för att det inte blir som man ritat.
I princip skulle Replisaurus maskin kunna användas för att tillverka även de undre ledarlagren i halvledarkretsarna där man idag använder en teknik kallad dual damascene.
– Vi skulle kunna ta oss in på den marknaden men ingen riskerar en fabrik för flera miljarder på ett uppstartsföretag. Då är möjligheterna mycket bättre för det översta ledarlagret.
Litografi och printning i samma steg Allt började under det år som Patrik Möller tillbringade på Berkeley i San Francisco. |
Men först måste kunderna övertygas om förträffligheten i tekniken och ännu är inte maskinen färdig. Replisaurus har idag tre team som jobbar med utvecklingen, ett för mastertillverkning, ett för maskinen och ett för kemin. Planen är att Rex II, den första kommersiella maskinen, ska vara klar i mitten av nästa år.
– Nu känns det som att det här kommer att gå. Principiellt fungerar det. Arbetet handlar mer om att beta av de problem vi har kvar.
En viktig pusselbit som föll på plats i fjol var när man köpte franska SET, Smart Equipment Technology, ett dotterbolag till Suss. Företagen samarbetade men förvärvet gav Replisaurus full kontroll över utvecklingen av själva replikeringsmaskinen.
– Det visade sig vara svårt att motivera någon annan att ta fram en maskin.
Förutom maskiner måste man få igång en kommersiell produktion av mastrar och kemikalier.
Det senare är enklast även om de elektrolyter som behövs är patenterade av Replisaurus så kommer de att tillverkas av de etablerade leverantörerna.
'
Idag finns det en utvecklingsmaskin i Kista där man kan demonstrera tekniken på åttatumsskivor. I praktiken är maskinen delad i tre delar, en för fyllning av mastern, en för rengöring och en för printningen där man flyttar skivorna manuellt.
Börjar testa med kunder i sommar
För att få upp yielden till uppåt 99 procent krävs en helt integrerad och automatiserad maskin. Den byggs nu tillsammans med teknikerna på Replisaurus-SET i Frankrike.
– Själva hjärtat är processkammaren och den utvecklar vi här i Kista. Vi är inne på sjätte generation och idag kan vi printa med bra uniformitet och yielden är i princip alltid över 90 procent.
Alla skivor testas och arbetet går helt ut på att stabilisera processen. För att komma in i en pilotlina krävs över 95 procents yield och för att nå produktionsvolymer krävs över 99 procents yield.
– Vi följer en kurva vi satt upp och har två till tre kvartal kvar dit.
Till sommaren kan man också ta emot potentiella kunder i Kista, kunder som kommer med egna wafers för att testa tekniken.
Själva maskinen byggs på en granitskiva som flyter på luftkuddar, det är för att kunna göra passningar mellan lagren på 0,25 µm till 0,5 µm vilket är bättre än vad maskpassare från till exempel Suss och EVG klarar idag.
Den kemiska processen är också på god väg och ska bli klar under tredje kvartalet. Även om den är aggressiv så inför den inga nya ämnen som inte redan finns i en halvledarfabrik.
För att få acceptans för maskinen och för att minska kostnaderna för företaget diskussioner med några halvledartillverkare om att de ska vara med och definiera maskinen och betala för utvecklingen
Rex II som den helt integrerade maskinen ska heta förväntas inte vara klar förrän under mitten av 2010.
Orubblig naturlag
Den första pilotproduktionen kan komma igång under andra halvåret 2010 men innan någon tillverkare vågar börja lova leveranser till slutkund är man inne på 2011. Först då skulle man kunna köpa en produkt som innehåller kretsar som tillverkats med en maskin från Replisaurus
– Då har det gått tio år sedan jag fick idén. Och det är det som alla har sagt till mig, det tar tio år och 300 miljoner att ta fram en ny halvledarteknik. Och det trodde vi absolut inte på då, säger Patrik Möller.