Internet of Things (IoT) är ett nätverk som är uppbyggt av ihopkopplade enheter, främst sensorer som sänder små datapaket. Det är värt att notera att de olika standarderna av sensornätverk är mycket väl förberedda för överföring av några eller ett dussintal bytes sensordata via sändare som matas med fritt tillgänglig energi.
Uppfinningen av ångmaskinen anses vara början på den första industriella revolutionen. Den andra hängde samman med uppfinningen av elektriciteten och förbränningsmotorn som gjorde det möjligt att automatisera många produktionsprocesser och effektivt transportera tillverkade produkter.
Den tredje var kopplad till utvecklingen av den digitala tekniken – uppfinningen av billiga datorer, mobiltelefoner och Internet. Den började under andra halvan av 1900-talet och gav upphov till den fjärde revolutionen som vi kan bevittna idag.
- IoT och IIoT
- Skillnader mellan IIoT och M2M
- Automationspyramiden
- Implementering som baseras på leveranser
Den fjärde industriella revolutionen är kopplad till begreppet Industri 4.0. Liksom alla på varandra följande är denna också kopplad till införandet och spridningen av tillämpningar för ny teknik. Den här gången handlade det om industrirobotar, artificiell intelligens, sakernas internet och dess undergrupp, sakernas internet inom industri. Å andra sidan kan man inte säga att orsaken till den fjärde industriella revolutionen bara var tekniska uppfinningar, utan samhällsförändringar och miljöhänsyn ligger också till grund för den. Nu lämnar vi de filosofiska övervägandena bakom oss och bara fokuserar på de tekniska aspekterna och på vad som kan hjälpa oss med de enskilda uppgifterna i industriella tillämpningar.
Det verkar som om drivkraften bakom alla de förändringar som sker idag (och inte bara inom tekniken) var uppfinningen av internet som ett globalt nätverk av enheter som ger en aldrig tidigare skådad möjlighet till kommunikation till låg kostnad och tillgång till kunskap och information över gränserna i alla dimensioner. I början användes internet i huvudsak för kommunikation mellan användare. Därefter introducerades åtkomst till multimedia och sedan började data från olika sensorer överföras via detta globala nätverk. Här finns det ett problem eftersom internet är perfekt anpassad för att överföra stora datapaket men hanterar dåligt små datapaket från sensorer som ofta innehåller mellan ett dussin bitar och ett dussin bytes. På Internet måste ett sådant paket åtföljas av en rad extra data som huvud och kontrollsumma som i detta fall är överflödiga och ofta tar upp mer utrymme än de faktiska mätresultaten som sänds av sensorn. En annan fråga är hur lång tid det tar för de att nå mottagaren och om data överhuvudtaget når fram eftersom de i extrema fall kan färdas en mycket lång väg eller gå förlorade. Det kan hända att de når mottagaren även med en fördröjning på flera sekunder vilket inte är något problem när man övervakar en godscontainer som transporteras från hamn "A" till hamn "B", surfar på en webbsida eller för ett e-postmeddelande men det är inte lämpligt för de flesta industriella tillämpningar. Ja, det är användbart på ledningsnivå eller för övervakning av de globala processerna men det är inte lämpligt för övervakning och styrning av produktionsprocessen.
För många personer som arbetar med industri och tillverkningsprocesser var tanken att utnyttja det globala nätverket i en industrianläggning eller logistik i samband med leveranser och transport mycket frestande. Därför utvecklades två tekniker som på sätt och vis är en delmängd av internet och som fick namnen Sakernas internet (IoT) och Sakernas internet inom industri (IIoT). Hur skiljer de sig från internet och varför bestämde man sig för att skilja dem åt?
Sakernas internet och Sakernas internet inom industri
Internet of Things (IoT) är ett nätverk som är uppbyggt av ihopkopplade enheter, främst sensorer som sänder små datapaket. Det är värt att notera att de olika standarderna av sensornätverk är mycket väl förberedda för överföring av några eller ett dussintal bytes sensordata via sändare som matas med fritt tillgänglig energi. I många tillämpningar sparar eller lagrar sensorgränssnittet energi genom att förbli vilande under långa tidsperioder för att sedan aktiveras enligt ett fast schema, med en viss frekvens eller på begäran.
Enskilda enheter som ingår i ett IoT-nätverk kan kommunicera med varandra och dela data via internet. Beroende på deras behov kan de anslutas via ett nätverk med varierad topologi. Viktigt är att dessa anslutningar upprättas med hjälp av olika standarder som främjas av oberoende tillverkare. I många tillämpningar används ett maskformigt nätverk vilket avsevärt ökar räckvidden och har en redundant anslutningsmekanism där data överförs via radio genom noder till en hubb. Maskformigt nätverk är dock inte regel utan sensorer kan också anslutas i ett nätverk med träd- eller blandad topologi. I ett sådant nätverk delar sensorerna data på begäran eller konkurrerar om tillgången till hubben.
Medan sensorerna själva inte är alltför komplexa och kan kommunicera med en intern standard måste hubben som är bryggan mellan dem och internet översätta data på lämpligt sätt och bilda standard datapaket. IoT-enheter används för att samla in, analysera och automatisera databehandlingen inom olika områden, bland annat energiproduktion och -distribution, styrning och övervakning av belysning, övervakning av transporter, väderförhållanden, floder eller hälsoskydd. IoT-tillämpningar som involverar olika typer av gränssnitt är mycket talrika och det kan förväntas att uppfinningsrikedomen i användningen av denna teknik fortfarande kommer att visa mer än en tillämpning. Detta är särskilt viktigt eftersom IoT kan vara och är förknippat med konsumentenheter.
Sakernas internet inom industri skiljer sig från sin prototyp främst genom sitt användningsområde. Det är ett nätverk av sammankopplade industrisensorer som inte bara kan kommunicera med varandra och asynkront bestämma startpunkter för de olika stegen i tillverkningsprocesserna utan även kan göra det möjligt att övervaka dem i realtid vilket hjälper maskinoperatörer och chefer att hantera fabrikerna på ett effektivare sätt. Information från enskilda styrsystem eller sensorer kan integreras och utvärderas av programvara som körs i molnet och som innehåller algoritmer för artificiell intelligens (artificial intelligence), maskininlärning (machine deep learning) eller processhantering. Dessa system gör det möjligt att uppnå en hög grad av integration mellan logistik- och tillverkningsprocesser vilket resulterar i ökad lönsamhet och konkurrenskraft för företaget.
IIoT-tekniken överbryggar klyftan mellan den operativa tekniken och informationstekniken, gör det möjligt att sammankoppla industriella processer och deras ledningssystem i nätverk och är ett viktigt verktyg för att stödja Industri 4.0-revolutionen.
Förväxla inte med M2M!
När man skriver om IIoT är det värt att nämna en kommunikationsteknik som kallas Machine-to-Machine, förkortat M2M, eftersom dess utveckling har varit central för förverkligandet av IIoT. Tidigare användes denna förkortning för att beteckna användargränssnitt men nuförtiden hänvisar den främst till länken maskin-till-maskin. Det är värt att notera att även om mottagaren av den information som genereras av maskinen är en människa skickas den fortfarande genom någon form av translator som är en maskin, så det handlar fortfarande om dataöverföring från maskin till maskin.
M2M är en teknik för dataöverföring mellan maskiner eller mellan en maskin och en så kallad nätverksnod (gateway) i en punkt-till-punkt-topologi. Nätverksnoden kan vara ansluten till ett företagsnätverk eller till ett globalt nätverk, t.ex. en mobiloperatör. I vissa tillämpningar särskilt där datakonvertering krävs kan gatewayen också förmedla i kommunikationen mellan maskiner.
M2M-tekniken är ganska svår att skala upp. Den rekommenderas särskilt när kommunikationen ska vara väl skyddad mot obehörig åtkomst och ökad tillförlitlighet krävs.Till exempel måste kommunikationen med en annan maskin eller operatör fungera även när ett internt nätverk eller en internetanslutning inte är tillgänglig. Till skillnad från IIoT tillåter M2M-kommunikationen inte att flera enheter synkroniseras i realtid eller styrs av en molnbaserad applikation. Den är också begränsad till en specifik standard för datautbyte, till skillnad från IIoT, där den skulle behöva säkerställa kompatibilitet med olika standarder eller utföra konvertering till en global standard. Därför är M2M-enheter inte en datakälla för ett företags ERP-, PLM- eller SCM-programvara.
På grund av skillnaderna i de två typerna av kommunikation skiljer sig också deras tillämpningsområde åt. M2M-tekniken handlar främst om maskiner, utrustning och slutenheter som smarttelefoner eller surfplattor, medan IIoT är förknippat med digitala enhetssystem som sensorer. Därför används M2M inom industrin huvudsakligen, t.ex. inom drift och underhåll för att varna om ett eventuellt maskinfel, underhållstid eller för att signalera skada, medan IIoT används för att integrera omfattande system. Det kan konstateras att M2M är mer inriktat på hårdvaran och IIoT på mjukvaran.
M2M-kommunikationen är utformad för att styra en enskild industrimaskin eller ett maskinkluster. Detta sker via radio- eller trådbunden kommunikation med användande av specialiserade M2M-hårdvarumoduler. Övervakningen sköts av en lämplig specialiserad enhet som sänder kommandon och tar emot data via den ovannämnda punkt-till-punkt-överföringen. IIoT-system använder internet för att sända data från sensorer eller enheter till molnet där flera tjänster och applikationer kan köras.
Termerna IIoT och M2M har gemensamma rötter eftersom de hänvisar till samma grupp av enheter. IIoT ger dock ytterligare möjligheter där traditionella M2M-system misslyckas. IIoT-system möjliggör datadelning inom företaget för att plocka ut affärsdata och hantera verksamheten på ett bättre sätt. Övergången från implementering av slutna silon till multifunktionella öppna IIoT-tekniker möjliggör dataintegration från sensorer och enheter med andra företagsapplikationer som Big Data och analys. M2M-system avkodar problem på maskinnivå eller inom serviceförbättring hos enheter medan IIoT-system utnyttjar Big Data och analys för att uppnå förbättringar i hela företaget.
M2M-system minskar kostnader i samband med externa tjänster tack vare fjärrfunktioner som fjärrdiagnostik, uppdateringar och fjärrfelsökning för att minimera antalet servicebesök till avlägsna platser. IIoT-system fokuserar däremot på operativa förbättringar och tillhandahåller informationsprodukter som en tjänst via molnet. IIoT innebär med andra ord övergången från hårdvara (som kommunikation och enheter) till mjukvara (som tjänster, praktisk kunskap och data) för att förbättra verksamheten.
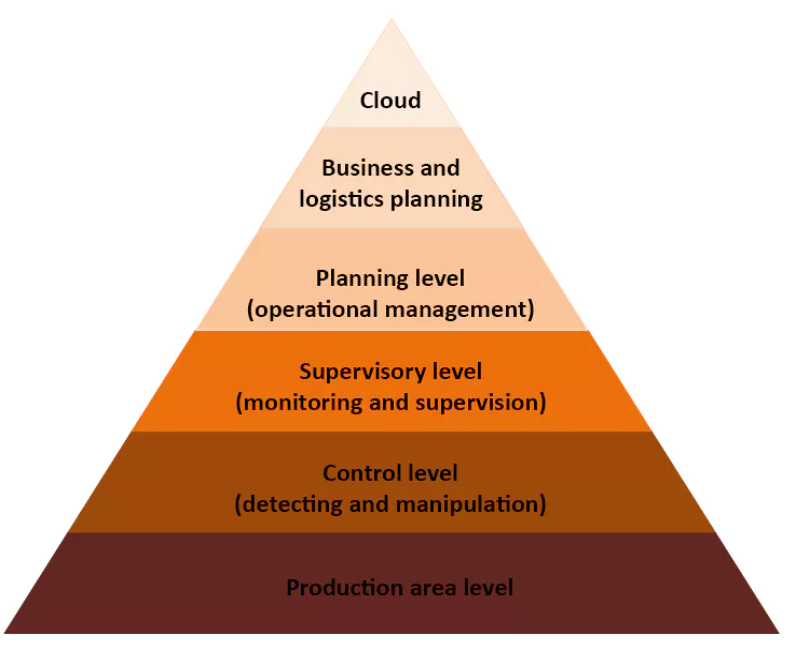
"Diagram för automationspyramiden inom industri 4.0 - upphovsman: Transfer Multisort Elektronik"
Automationspyramiden på företaget
Teknik som är kopplad till M2M, IoT eller dess särskilda version IIoT kan vara tillräcklig för att automatisera produktionsprocessen men den är fortfarande lång ifrån den revolution som nämndes i inledningen. Revolutioner kan utlösas av nya idéer som ifrågasätter den rådande ordningen och föreslår alternativa lösningar. När man planerar automatisering av ett företag enligt principerna för Industri 4.0 kan man ta hjälp av ett diagram som oftast presenteras i form av en så kallad automationspyramid. Låt oss diskutera de olika nivåerna i denna pyramid.
Nivå 0 – Produktionsnivå/Produktionsprocess
På nivå 0 finns enheter, manöverdon och sensorer som används i området som omfattas av produktionsprocessen. Detta område bör inte endast identifieras med en fabrikshall eftersom ventiler som styr flödet ofta installeras utanför den, t.ex. i utlopp från tankar som levererar råvaror för produktion och är monterade utanför hallen. Andra exempel av sådana enheter eller sensorer är pumparnas elektriska motorer, hydraulcylindrar eller närhetssensorer för detektering av objekt eller deras förflyttning som fyller liknande funktion som fotoelektriska strömbrytare o. dyl.
Nivå 1 - Kontrollnivå/Detektering och manipulering
Det är en nivå med manipulering och bearbetning av fysiska objekt. Här styrs och kontrolleras PLC-styrenheter och PID-regulatorer. Verktyg och manipulatorer som är anslutna till dem utför den verkliga bearbetningen med hjälp av olika sorters teknik. Dessa PLC-styrenheter och PID-regulatorer hämtar information från sensorer, strömställare och andra ingångsenheter för att fatta beslut om vilka utgångar som ska aktiveras för att slutföra en inprogrammerad uppgift.
PLC-styrenheter innehåller processor, minne för lagring av programvaran och annan data samt in- och utgångsmoduler. PID-regulator är oftast integrerad med en PLC-styrenhet eller utförd i form av ett lämpligt program som verkställs av PLCn. En vanlig industriell process som styrs med PID är temperaturreglering. Många tillverkningsprocesser kräver uppvärmning eller kylning och upprätthållande av en viss tillåten marginal för temperaturvariationer.
Nivå 2 – Övervakningsnivå/Övervakning och tillsyn
Denna nivå kallas övervakningsnivå. Den använder SCADA-programvara (termen SCADA kommer från de första bokstäverna i orden Supervisory Control And Data Acquisition). SCADA är en kombination av de tidigare nivåerna som ger tillgång till data och hantering av produktionsprocesser med system som möjliggör kontroll och styrning från en enda plats. Vanligtvis installeras ett grafiskt användargränssnitt här som möjliggör fjärrstyrning av funktioner. Med hjälp av SCADA kan flera system övervakas och styras från en och samma plats. Det är inte begränsat till en maskin, process eller enhet.
Nivå 3 – Planeringsnivå/Operativ ledning
Den fjärde nivån i automationspyramiden (räknat från 0) kallas planeringsnivå. På denna nivå används ett datoriserat ledningssystem som är känt som MES (Manufacturing Execution System). MES övervakar hela produktionsprocessen i en anläggning eller fabrik, från leveranser av råmaterial till den färdiga produkten. Tack vare det får fabriksledningen en fullständig bild av vad som händer under produktionen och kan fatta beslut baserat på denna information. Det är t.ex. möjligt att justera beställningar av råmaterial eller leveransplaner för färdiga produkter baserat på de faktiska data som erhålls från systemen.
Nivå 4 – Affärs- och logistikplaneringsnivå
På toppen av pyramiden finns ledningsnivå. Det använder ett integrerat system som betecknas med förkortningen ERP (Enterprise Resource Planning). Med hjälp av detta system kan företagsledningen övervaka och styra verksamheten. Förkortningen ERP täcker vanligtvis en uppsättning olika datorprogram som samlar in, bearbetar och övervakar allt som händer i företaget. ERP utnyttjar information som finns tillgänglig på de lägre nivåerna i pyramiden och ytterligare programvara som integrerar de data som de gör tillgängliga. På så sätt kan alla nivåer av företagets aktivitet övervakas, från resurser, genom produktion, produktdistribution, inköp, ekonomi och löner och mycket mer.
Nivå 5 - Molnet
Molnet är en term som är en direkt översättning från det engelska språket som inte särskilt bra återger den faktiska betydelsen av detta område. Molnet är helt enkelt ett kluster av enheter och de applikationer som körs på dem och som möjliggör en djupgående datainsamling, -integrering, -utvärdering och -behandling. Data kan sänds till molnet från vilken nivå som helst i automationspyramiden. I detta moln kan de samlas in, behandlas och utvärderas av programvara för artificiell intelligens som stöds av maskininlärningsmekanismer. Egentligen så är det först molnet och däri tillgängliga mekanismer som gör det möjligt att uppnå en högre nivå av effektivitet och operativ perfektion.
Omvandlingen av ett företag till den form som krävs av Industri 4.0 innebär många tekniska och organisatoriska förändringar. Den kräver tid och tekniska resurser och kan realistiskt sett inte genomföras på kort tid. Därför är det värt att dela upp den i etapper och sätta upp specifika, verkliga mål och sträva efter gradvisa förändringar. Det är också värt att fokusera på lokala lösningar innan de skalas upp till globala, främst genom att ta ut nödvändig information som finns tillgänglig lokalt och skapa applikationer som tar hänsyn till användningsfallen för dessa data. Med detta i åtanke kan man identifiera tre steg i omvandlingen:
- Digital kommunikation och sensorer: Syftet med denna etapp är att sträva efter högsta möjliga effektivitet och operativ perfektion. Denna fas kommer därför att omfatta förbättringar av produktiviteten, kvaliteten och effektiviteten samt bättre riskhantering genom integration och automatisering, IoT-lösningar, artificiell intelligens, molnet och avancerad analys. Införandet av IoT innebär att ett digitalt nätverk måste byggas upp och att information matas in i det från ett stort antal sensorer. Nätverkets effektivitet och hastighet kommer i hög grad att avgöra om fördelarna med Industri 4.0 kan utnyttjas fullt ut eftersom det "digitala" företaget inte kommer att kunna fungera effektivt utan tillförlitlig dataöverföring.
- Digital ingenjörskonst: Syftet med dess användning är att förbättra tillväxten. När grunden är lagd kan man börja leta efter fördelar djupare med hjälp av den teknik som finns tillgänglig inom ramen för Industri 4.0 i syfte att förbättra projekteringsprocessen och leveranskedjorna. Inom vissa produktgrupper kan man också försöka utveckla så kallade smarta produkter som skapar vissa ekosystem inom vilka kommunikation sker och data överförs. Ingenjörskonst omfattande smart automation och smarta kontrakt baserade på blockchain-tekniken kan vara aktuell. Ett sådant ekosystem kan påverka tillverkningsprocessen och leveranskedjan vilket ger ytterligare optimering av ett företags rörelsekostnader.
- Digitala operationer: Syftet är att få en större variation. Den sista etappen inträffar när företaget är helt digitalt och kräver användning av Industri 4.0-möjligheter för att säkerställa en verklig konkurrensfördel. Införande av de förändringar som nämndes tidigare i alla etapper från design till färdig produkt kommer att ge företaget möjligheten att kunna snabbt reagera på marknadens behov och skapa unika produkter. Det kommer också att underlätta respons på målmarknadens omdömen vilket möjliggör ännu bättre, effektivare och snabbare svar på dess behov. Det är dock värt att notera att variationen inte bara handlar om att särskilja ett företag från dess konkurrenter utan även kan skapa helt nya marknader, tjänster och affärsmodeller.
Tillgången till material och komponenter är nyckeln till revolutionen
När ett företag bygger sin egen automationspyramid och söker efter nödvändiga tekniska lösningar är det inte bara enheter som routrar utan även små elektroniska och elektromekaniska komponenter som kontrollampor, sensorer, kontaktdon och flera andra som efterfrågas. Dessa kommer att behövas för nätverksinfrastrukturen, maskin-till-maskin-anslutningar, gränssnitt för att signalera maskinens status till operatören osv. I sådana fall är det värt att förlita sig på en beprövad partner som på kort tid kan förse företaget med nödvändiga komponenter. TME är en beprövad partner. Företaget har funnits på marknaden sedan 1990 och har arbetat med materialdistribution och -leveranser sedan verksamhetsstarten. Servicestandarden har bekräftats med ISO 9001:2015- och ISO 14001:2015-certifikaten och sortimentet omfattar ett brett urval av komponenter som krävs för en fullständig implementering av Industri 4.0.
Texten är framtagen av Transfer Multisort Elektronik Sp. z o.o.
Länkar: